Crushed sand is also known as Manufactured sand (M-Sand).
These sand is cubical with grounded ends, washed, and graded for use as a material for construction.
In this article you’ll learn:
- What is crushed sand?
- Types of crushed sand.
- Merits and Demerits of the crushed sand.
- Lots more.
So, if you’re ready to go with crushed sand, this article is for you.
Let’s dive right in.
What is Crushed Sand?
Crushed sand is a replacement for river sand in a concrete building.
When Crushing hard granite stone produces manufactured sand.
The manufactured sand (M-Sand) size is reduced to less than 4.75mm.
Purpose of Crushed Sand:
- Crushed Sand is used instead of natural sand since the desire for sand has surged due to the fast-increasing construction projects, resulting in a lack of appropriate river sand throughout most regions of the world.
- Crushed sand of the scarcity of high-quality river sand for building, the usage of artificial sand has grown.
- Using M-Sand is its ease of access and low shipping costs.
- Manufactured sand may be crushed using solid granite rocks, and it can be found in the area, saving money on transportation from a nearby river sand bank.
- Thus, the use of synthetic sand as an alternative construction material can help to keep construction costs under control.
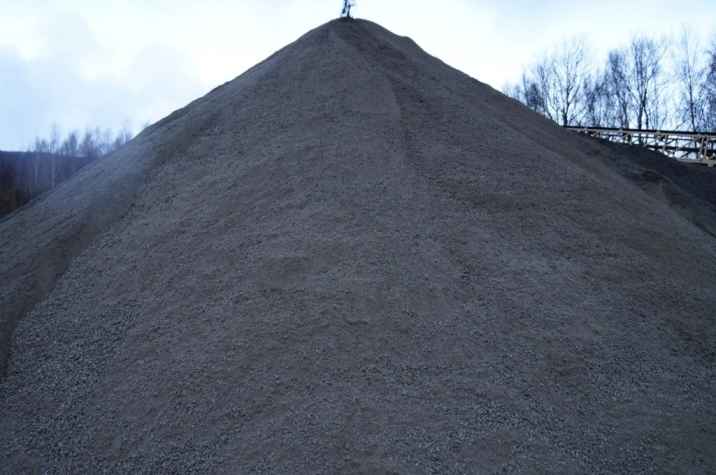
Types of Crushed Sand:
M Sand for Concreting:
Screening size or granule thickness is 150 microns – 4.75 mm. It complies with IS code 383: 1970.
M Sand for Plastering:
This sand is often used in tiling and plastering. The thickness of the granule or the size of the sieve is 150 microns – 2.36 mm. It complies with IS code 1542: 1992.
M Sand for Brick or Block Work:
This sand is commonly used in masonry, brickwork or block laying operations. The thickness of the granule or the size of the sieve is 150 microns – 3.55 mm.
Process of Manufacturing Crushed Sand:
The main procedure for producing crushed sand is as follows:
Extraction
Crushing Aggregate
Sorting and screening
Air recognition
Handling and storage
Manufactured sand is created by passing hard stones of various sizes via primary and secondary crushers (Jaw crusher and Cone crusher), reducing the particle size to those of sand.
Because of its unique design and attrition action, the VSI crusher generates cubical and angular fine aggregate particles.
The attrition process can also reduce the surface roughness of fine aggregates to a certain amount.
During the manufacturing process, sand stockpiles are checked to verify that they are not polluted by gnarled changed rock, clay, or other impurities.
Crushing numerous source rocks into a single sand stockpile is also prohibited unless such a method can be proved to be under blending control and generates a consistent output.
Manufactured Sand facilities ensure correct grading for improved particle size distribution due to the built-in process of multiple stages of screening.
By cleaning, the proportion of micro fines (those smaller than 75 microns) is kept below 15% by weight.
The washing equipment also ensures that the manufactured sand remains moist or partially wet.
This will aid in lowering the water absorption rate of manufactured sand during the concrete making, resulting in improved workability and strength, and durability retention.
Properties for Crushed Sand in Concrete Construction:
Concrete with Higher Strength:
The produced sand has the needed fineness gradation, physical features such as form, smooth finish textures, and consistency, making it the ideal sand for building.
Sand’s physical qualities increase concrete strength by minimizing segregation, bleeding, efflorescence, gaps, and capillary.
Concrete’s Durability:
Crushed sand (M-Sand) is created from high-quality granite and has regulated physical and chemical properties that are appropriate for concrete structure construction.
This M-Sand feature helps concrete buildings endure harsh weather conditions and avoids reinforcing steel corrosion by lowering permeability, moisture ingress, and the freeze-thaw impact, hence enhancing the lifetime of concrete structures.
Concrete Workability:
The workability of concrete is affected by its size, shape, and texture.
As the total area of sand grows, so does the requirement for cement and water to connect the sand to coarse aggregates.
Controlling the physical qualities of manufacturing sand allows the concrete to use less water and generate more workable concrete.
Construction Defects:
The use of M-Sand, which has an appropriate initial and final setting time as well as high quality, reduces construction difficulties such as segregation, bleeding, granulation tissue, holes, and capillarity in concrete.
Economy:
As previously stated, the use of M-Sand has greater durability, higher strength, reduced segregation, permeability, increased workability, and lower post-concrete flaws, proving to be cost-effective as a building material replacement for river sand.
In many circumstances, it can also save on river sand transportation costs.
Eco-Friendly:
The use of manufactured sand eliminates the dredging of river beds to get natural sand, which may result in environmental disasters such as groundwater depletion, water shortages, threats to the stability of bridges and reservoirs, and so on.
Advantages of Crushed Sand:
- Crushed Sand possesses balancing physical and chemical properties that can withstand harsh climatic conditions.
- It has been rated correctly in the required percentage.
- Flexural and compressive strength is also improved.
- M-Sand is extracted from a specific hard rock (granite) utilizing cutting-edge international technology, resulting in the needed sand property.
Disadvantages of Crushed Sand:
- The angular grain or flaky particles produced by poor crushing may necessitate more water and cement, rendering it unsuitable for concrete production.
- Due to the higher costs of river sand, the lack of suitable crusher setup in some regions of the nation, such as West Bengal, might be a concern.
- Regarding high-grade pumpable concrete in high-rise buildings, cement is required in greater quantities than the river sand, which may be prohibitively costly.
Also read: Difference Between M Sand and River sand | Fine Aggregates | Types of Sand
Conclusion:
As previously said, crushed sand has several properties such as greater durability, better strength, reduced segregation, and permeability, and it is proving to be cost-effective as a construction material in place of river sand.
In a subsequent post, we will go over additional technical aspects of produced sand.
Related Posts
Rock Quality Designation(RQD): Building Strong Foundations
Spread Footing
Masonry Cement
Plain Cement Concrete
Concrete Efflorescence
Concrete Pile
Stepped Footing
Fineness Modulus of Coarse Aggregates
Difference between Condo and Apartment