A diaphragm wall is a long-lasting reinforced concrete wall built into the ground to support large-scale construction projects like dams, tunnel concepts, deep basements, and enclosures.
They serve as a retaining wall, a foundation, support for the underground structure or a means of cutting off access to allow for deep excavation.
In this article you’ll learn:
So, if you’re ready to go with a diaphragm wall, this article is for you.
Let’s dive right in.
What is Diaphragm Wall?
A diaphragm wall is a rectangular section that is built in place beneath the soil.
These walls are constructed panel by panel both interlocked to guarantee structural stability and water tightness.
The diaphragm walls’ thickness can range from 60 cm to 150 cm, and their width can be between 2.0 and 3.5 meters.
Diaphragm walls can be built down to a depth of 60 meters.
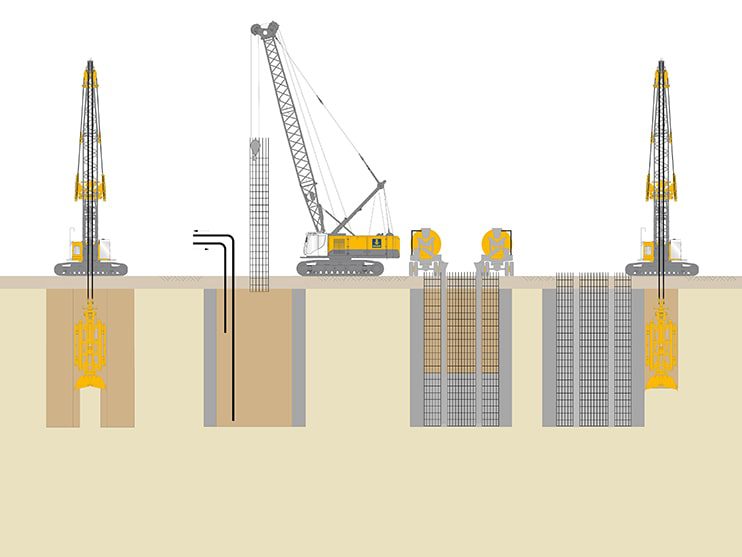
Purpose of Diaphragm Wall:
- In order to build a cast-in-situ reinforced concrete retaining wall, diaphragm walls are also known as slurry walls or slurry trenches.
- These walls offer a rigid, economical solution for shafts and permanent retaining walls with fewer construction joints.
- Diaphragm walls are frequently used in crowded areas, close to existing structures and in places with limited headroom, or when an excavation is being done to a depth where much more soil would otherwise need to be removed in order to create stable battered slopes.
Types of Diaphragm Wall:
1. Grabbed Diaphragm Wall:
To create a continuous cut-off, retaining, and/or structural wall, vertical panels are excavated below stabilizing slurries using mechanical/hydraulic clamshell grabs or hydromel cutters.
In densely populated areas or in situations where very deep excavations are necessary to create stable battered slopes, diaphragm walls are ideal.
Ideal for deep basements, underground rail stations, rail car unloaders, tunnel approaches, pumping stations, and similar applications
The assistance for top-down or open excavations.
Put up obstacles to groundwater flow, supplying weight-bearing components.
2. Slurry cut-off walls:
Deep underground non-structural obstacles called slurry cut-off walls are used to stop groundwater flow along either groundwater table.
They can be used to stabilize dams and levees, dewater excavation places, and contain polluted water at waste disposal sites.
Cut-off walls are typically 1.5 to 5 feet wide and inserted a few feet into bedrock or clay with low permeability.
Backfill for slurry walls is bentonite, which can contain dug-up soil or cement.
3. Sheet pile wall embedded in the cut-off wall:
All types of water retention constructions use sheet pile cut-off walls to reduce the exit gradient at the downstream toe and prevent sand boiling and piping.
Utilizing a rigid guide frame or “framework” into sheet piles, sheet piling panels are threaded together prior to being piled.
This enables the architectural elements of the sheet pile wall, which is especially significant in very soft soils where swaying can be a problem.
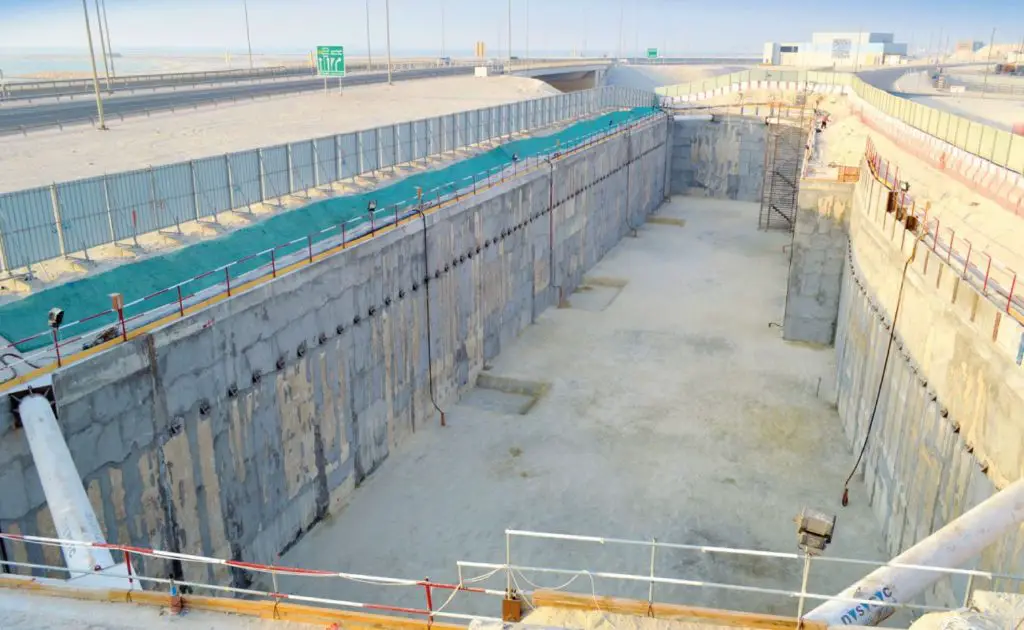
Construction Procedure:
1. Site Logistics and Slurry Plant Setup:
Setting up a diaphragm wall requires a space large enough for setting up the slurry plant and putting the reinforcing cages together before they are put inside the wall.
In congested areas, this work may be difficult.
Prefabrication is an choice for reducing the area required for the site cage.
A slurry mixer, storage containers, and descending entities make up the slurry plant.
For bentonite slurry hydration, adequate storage tanks must be used.
2. Pre-trenching:
This procedure is used to remove shallow obstructions and to provide stable support for guide walls.
This is completed as an open excavation that is backfilled with flow fill/ excavated with self-hardening slurry.
3. Construction of Guide Walls:
Guide walls act as a template for wall excavation panel layout, support the top of trenches, restrain end slopes act as a basis to hang reinforcement.
It is provided reference elevation for inserts, support tremie pipes, hold down cage during concreting, and react to jacking out some end slope types.
For construction to be completed in a dry environment, guide walls made of reinforced concrete must have a top with 4 feet above the groundwater table.
4. Panel Excavation (Vertical Segment):
Panels are unique rectangular clamshells that are used to create vertical slots, they are also referred to as grabs or buckets.
Digging equipment may be hydraulic or cable-operated.
In panels that are divided vertically, the excavation is done.
The primary sources of trench stability are the bentonite’s fluid weight and the arcing action of the soil surrounding the trench.
Bentonite slurry is started pouring into the pit and kept at least 3 feet just above the groundwater table and then within 2 feet of the top of the guide wall for the diaphragm wall.
5. Stop End Placement:
Stop Ends are used to regulate the placement of concrete so that adjacent panels are not excavating monolithic concrete when they are next to each other.
The end stop can be fixed in place or removed after pouring concrete.
Wide flange end-stops are the standard for permanent end stops.
Pipe or special keyway end stops can be used as a removal end stop.
6. Single-use PVC pipes:
This technique places two pipes at the ends of the steel reinforcement cage of the panel.
The primary panel is concretized, leaving the pipes filled with slurry.
The separation is broken as the second panel is concretized with a special tool.
7. Panel Descending:
The panel may descend to remove extra sand from the bottom panel and slurry.
Sand removal from slurry reduces its density, preventing pockets of sand from forming or mixing with tremie concrete.
8. Insertion of the Reinforcing Cage:
Concrete is poured around the reinforcing cage using tremie techniques to create the concrete panel.
9. Tremie Concrete:
Tremie pipes are inserted into the bottom of the panel, and 8 to 10 inches of slump concrete is trimmed into the panel.
Concrete mixes typically have a fairly high cement content as well as other pozzolana, plasticizers, and chemicals.
They also provide 4000-6000 psi strength with a high slump.
Advantages of Diaphragm Wall:
- A diaphragm wall has fewer joints than a secant wall ultimately improves the water tightness of the wall.
- Since they can be built to withstand extremely high structural loads, diaphragm walls are frequently used to hold back extremely deep excavations.
- The wall construction process is relatively quiet and vibration-free.
- The wall can be built to extremely deep levels (in excess of 80m).
- Diverse types of rocks and soil can be used to construct the Diaphragm Wall.
- Since the wall is watertight and doesn’t need to be dewatered, it barely affects nearby structures.
- The wall acts as the foundation for the superstructure as well as an exterior wall for the basement.
Disadvantages of Diaphragm Wall:
- When compared to other types of excavation support systems, diaphragm wall construction is relatively expensive owing to the requirement for excavating and pumping equipment.
- Strong soil conditions with slow and difficult penetration do not suit the construction of diaphragm walls.
Uses of the Diaphragm Wall:
- In places with substantial and older urban infrastructure.
- Where the need for a very rigid earth retention system exists.
- They are utilized when it is necessary to minimize noise and vibration.
- When dewatering is not a choice.
- Where geology and groundwater prevent the use of a conventional earth retention system.
Also read: Load Bearing Wall | CMU Walls | Frost Wall
Conclusion:
Diaphragm walls are stiff in terms of controlling ground movement compared to other wall types.
When a low permeability layer lies beneath granular soil in granular soils with high groundwater tables, diaphragm walls are frequently attractive.
Diaphragm walls in an underlying low permeability layer is made up of soil or rock.
This reduces groundwater seepage beneath the wall.
Related Posts
Rock Quality Designation(RQD): Building Strong Foundations
Spread Footing
Masonry Cement
Plain Cement Concrete
Concrete Efflorescence
Concrete Pile
Stepped Footing
Fineness Modulus of Coarse Aggregates
Difference between Condo and Apartment