Hydrophobic cement contains admixtures that minimize the wettability capacity of cement grains.
These materials surround the cement grains in a thin film.
When the Portland cement clinker is ground with a film-forming substance, such as oleic acid, the result is hydrophobic cement, which slows the rate of deterioration when the cement is stored in unfavourable conditions.
The absorption films are uncertain off the surface of hydrophobic cement when water is added, and they in no way obstruct cement’s normal ability to harden.
In this article you’ll learn:
So, Let’s dive right in.
Introduction of Hydrophobic Cement:
Hydrophobic concrete is water-repellent concrete, it is compliant with the requirements stated in the definition of waterproof concrete.
Since its invention in Australia in the middle of the 20th century, millions of cubic yards of hydrophobic concrete have been poured in Asia, Europe, Australia, and the United States.
Its widespread acceptance and expanding use have been facilitated by its successful application in hundreds of structures.
The initial strength gain is minimal because hydrophobic coatings on some grains keep them from coming into contact with water.
Its strength is comparable to regular Portland cement after 28 days.
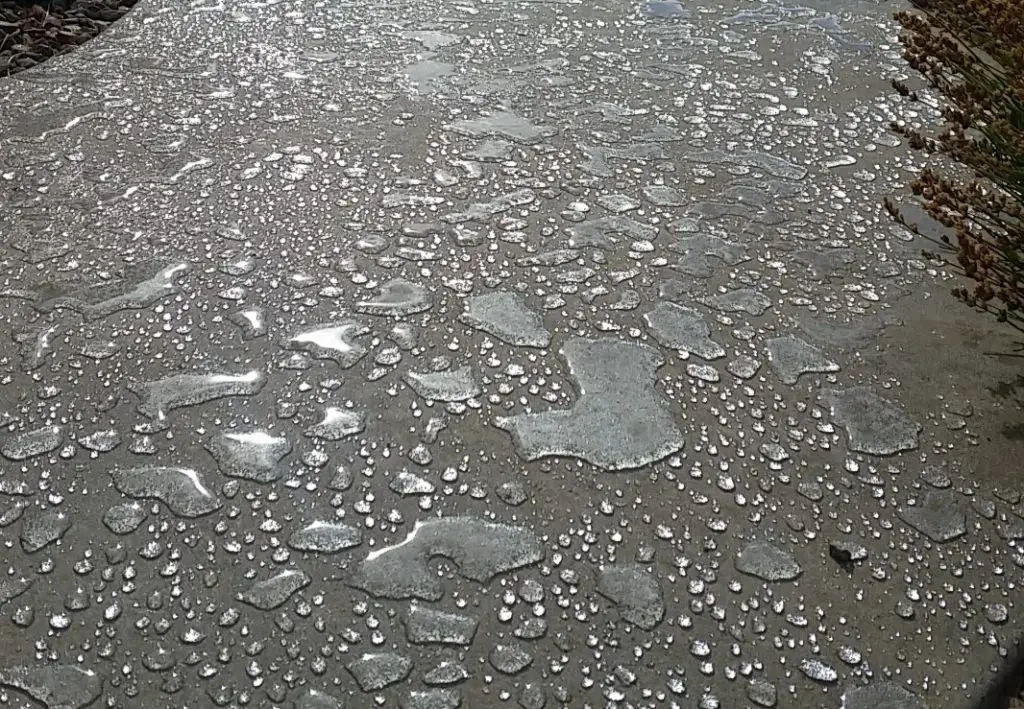
Manufacturing of Hydrophobic Cement:
This specialty cement is made using the same process as Portland cement.
When making cement, the clinkers are ground with a water-repellent film substance like oleic acid or stearic acid.
In the course of transportation or storage, these chemicals layer on the cement particle THAT prevents water from mixing with it and beginning the hydration process.
The vigorous mixing causes this layer of water resistance to break down, allowing hydration to occur.
Properties of Hydrophobic Cement:
Properties | Value |
Fineness | |
Soundness Lechatelier (mm) Autoclave | 10mm 0.8 % |
Setting Time Initial Setting: Final Setting: | 30min 600min |
Compressive Strength 3days 7days 28days | 16 MPa 22 MPa 30 MPa |
Water Absorption | 0.3 – 1 % |
Advantages of Hydrophobic Cement:
- The primary features of hydrophobic cement are as follows:
- Make long-lasting repairs with high-quality materials.
- The strength is equivalent to regular cement.
- Usually, three minutes after being mixed with water, quickly sets and hardens.
- Within an hour of application, painting is possible due to the quick setting and hardening times.
Disadvantages of Hydrophobic Cement:
- The principal issues with hydrophobic cement are as follows:
- Not effective on frozen surfaces.
- It cannot be used in climates with temperatures below 40 °f.
- Leakage issues are resolved by this cement, but condensation-related issues are not resolved.
- This type of cement requires skilled labour and a favourable climate for its use.
Precautions for Hydrophobic Cement:
- Don’t breathe the dust in.
- Avoid making contact with your skin or eyes.
- Despite the fact that there is little proof that silica is a carcinogen, inhaling it may cause lung issues.
- Wearing safety equipment is advised, such as gloves or a mask.
Applications of Hydrophobic Cement:
- This cement is used in climates with prolonged wet periods and longer storage times.
- It is used primarily in tunnel construction because underground repairs are challenging and expensive.
- These cements are employed in the building of dams, spillways, and submerged structures.
- Also, used in structures with green roofs, other types of roofs, parking garages, and public spaces that are subject to precipitation or rain puddles.
- It is used in manholes and drainage construction.
- Used in dams, retaining walls, and water treatment facilities.
- It can repair cracked foundations and dripping pipes without having to stop the dripping.
Also read: Reactive Powder Concrete | Portland Slag Cement (PSC) | Blended Cement
Conclusion:
By using chemicals, a hydrophilic cement mortar surface can become hydrophobic.
Iso-octyltriethoxysilane produces consistent self-assembled molecular films on the surface of hydrated products through condensation and hydrolysis.
The coats the surface of the mortar with a hydrophobic coating has a thickness of 1-3 mm.
Related Posts
Rock Quality Designation(RQD): Building Strong Foundations
Spread Footing
Masonry Cement
Plain Cement Concrete
Concrete Efflorescence
Concrete Pile
Stepped Footing
Fineness Modulus of Coarse Aggregates
Difference between Condo and Apartment