Ordinary Portland cement (simply called Ordinary Cement) refers to the hydraulic binding material by mixing the appropriate amount of Portland cement clinker, composite material, and gypsum, this cement is excellent binding properties that give strength to structural elements.
Portland pozzolana cement is finer than ordinary Portland cement due to pozzolanic action.
Here we will learn about ordinary portland cement, types of Ordinary portland cement & ordinary portland cement composition in detailed.
Introduction to ordinary Portland cement:
Ordinary Portland cement is one of the most widely used cement.
The name Portland cement was given by Joseph Aspdin in 1824 due to its similarity in colour and high quality when it hardened like a Portland stone.
Portland stone is white grey limestone within the island of Portland, Dorset.
Types of ordinary portland cement:
There are two methods for manufacturing of cement as follow:
Wet manufacturing process:
- In this method, mixing and grinding of raw materials is done in a wet state.
- All raw materials are transported to a ball mill or tube mill and they are ground to a consistent consistency of the solution with the addition of water.
- The solution is tested to give the required chemical composition for time to time.
- Finally, the modified slurry is stored in the final storage tank.
- The corrected slurry is fed into Rotary kiln, where at 1500 °C temperature given to the slurry to form with the clinker.
- The clinker falls into the rotary cooler & cooled under controlled conditions.
- Cooled clinker is added to a ball mill of 3 to 5% gypsum to prevent flash-setting of cement.
- Then portland cement is stored in cement silos and finally dispatched or filled into barrels for bulk supply to dams or other large works.
Dry manufacturing process :
- In this method, the raw material is dried, crushed and fed to the grinding mill in the correct proportion.
- The raw materials used for cement manufacture are limestone and clay.
- The dry powder called raw metal is then re-mixed and correct composition are mixed through compressed air.
- The mixture is fed into a large rotary kiln in which it is heated to a temperature of 1450 °C in a dry state.
- The chemical reaction in kiln causes the material to aggregate into clinker.
- The hot clinker is then cooled up to 100 °C at which it can easily be stored in clinker silos.
- Then add 3 to 5 % gypsum to form a fine powder and retard the setting time, finally dispatched in a bag of 50 kg.
Manufacturing process of ordinary portland cement:
The cement manufacturing process can be divided into three distinct stages as follows;
Raw material acquisition:
The raw materials required for the manufacture of Portland cement are calcareous (such as limestones and chalks) and argillaceous material such as shales, slates or clays.)
Clinker production:
Clinker is produced in a Kiln.
Grinding, mixing and burning of raw materials at a temperature at 1400 – 1500° C.
Clinker is produced in a kiln in the form of dark greenish-blue balls.
Cement grinding, packing and distribution:
The clinker is cooled and ground to a fine powder by adding 3 to 5% gypsum.
Then packing and storage of the product.
The product formed using this process is Portland cement.
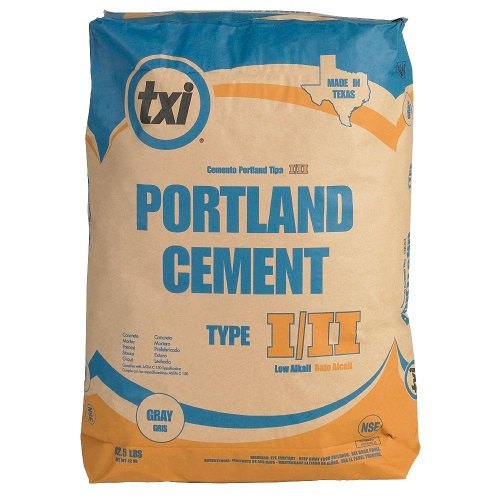
ordinary portland cement chemical composition:
Lime:
Deficiency of lime causes a decrease in the strength of cement and excess free lime causes unnecessary expansion and disintegration of cement.
Proper percentage of lime maintains the binding property of cement.
Silica:
During the manufacturing of cement, silica undergoes a chemical reaction with calcium to form di-calcium and tri-calcium silicates which adds strength to the cement.
The high amount of silica provides strength to the cement, but its setting time is delayed.
Alumina:
A large amount of alumina accelerates the setting but weakens the cement.
Iron Oxide:
The high volume of iron oxide will make the cement difficult to fuse and form clinker.
High ferric oxide content is favourable to the production of high early strengths in cement.
Magnesia:
The magnesium content shall not exceed 5.0 % by mass.
Excess magnesia makes the cement unsound.
Sulphur Trioxide:
Excess quantity of sulphur trioxide also makes the cement unsound.
Alkalies:
The large quantity of alkalies causes efflorescence.
Cement with lower alkali content has caused objectionable expansion.
Gypsum:
During the grinding process, a small quantity of gypsum is added.
Gypsum increase the setting time of cement.
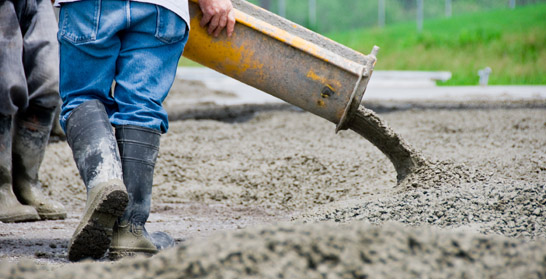
Advantages of ordinary portland cement:
- OPC has great resistance to cracking and shrinkage.
- The initial setting of OPC is faster than that of PPC.
- The treatment period of OPC is shorter than PPC hence the cost of treatment is reduced, therefore recommended where the cost-prohibitive treatment will occur.
Disadvantages of ordinary portland cement:
- It cannot be used for large-scale concreting because it has a higher heat of hydration than PPC.
- The durability of OPC is lower than the PPC.
- It produces relatively less solid concrete than PPC, so pumping the concrete becomes a bit difficult.
- The OPC is finer hence higher permeability and consequently lower durability.
- OPC is expensive than PPC.
Application of Ordinary Portland Cement:
Type I: For general purpose.
Type IA: It is similar like Type I, but when air entrainment is desired.
Type II: For moderate sulfate resistance.
Type IIA: It is same as Type II, but when air entry is desired.
Type II (MH): It is much like Type II, but when moderate heat of hydration is desired.
Type II (MH) A: Similar to Type II (MH), but when air entrainment is desired.
Type III: For high starting power.
Type IIIA: Alike to Type III, but when air entrainment is desired.
Type IV: For low heat of hydration.
Type V: for high sulfate resistance.
Uses of ordinary portland cement:
- It is used for general construction purposes, where special properties are not required like reinforced concrete buildings, bridges, etc.
- Also used in most concrete masonry units.
- It is also used as a basic component in mortar, plaster, and non-specialty grout.
Also read: Quick Setting Cement, White Portland Cement & Hydraulic Cement
Conclusion:
Ordinary portland cement is a complex product derived from unprocessed common natural materials like limestone and clay.
Therefore it is necessary for the cement industry to produce clinker that would facilitate the production of low w/c concrete that are more durable than general strength concrete.
Good and useful information on Ordinary Portland Cement and PPO.