Rapid hardening cement is a unique kind of cement that hardens quickly and develops great strength.
Typically, conventional cement takes 7 days to reach the same strength that they do in 3.
High-Early Strength Portland Cement is another term for this kind of cement.
Rapid Hardening Cement (RHC) is a specific type of Portland cement widely used in concrete buildings to reach high strength earlier than Ordinary Portland Cement (OPC).
In this article you’ll learn:
So, if you’re ready to go with it, this article is for you.
Let’s dive right in.
Introduction to Rapid Hardening Cement:
According to AASHTO M 85 specification and ASTM C 150 standard specification for Portland cement.
RHC is categorized as a type-III cement and it is also known as High Early Strength cement.
In contrast, quick-setting cement simply sets earlier but hardens more quickly than OPC.
It refers to the fact that assuming the same water-to-cement ratio has been used.
This cement achieves the same strength that OPC does in 7 days.
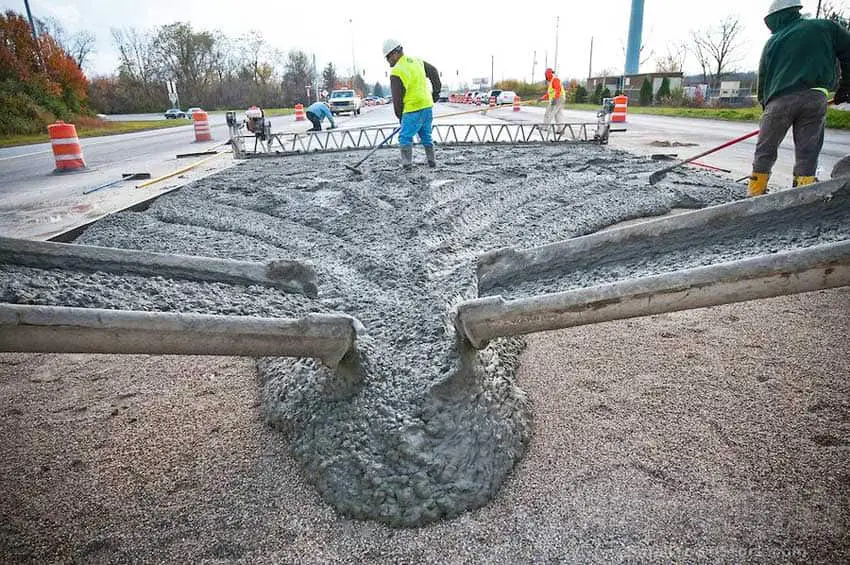
Properties of Rapid Hardening Cement:
- It grows stronger more quickly than OPC.
- With the same water-to-cement ratio, OPC gains 7 days’ worth of strength in just 3 days.
- Its final setting times are 30 minutes and 600 minutes, which are the same as OPC.
- This cement is inappropriate for bulk concreting since it emits greater heat while setting.
- This cement has autoclave soundness of 0.8% and a Le Chatlier’s soundness of 10mm.
- It has a specific surface area greater than 3250 cm2/gm.
- This cement is more expensive and lighter than OPC.
- It is cost-effective because of its quick curing time.
Manufacturing of Rapid Hardening Cement:
Rapid hardening cement is made using the dry manufacturing process for cement.
Limestone and shale are utilized as raw materials in this cement, and they are burned to an incredibly high temperature to create clinkers.
To create this cement, the lime and shale clinker is combined with a little amount of gypsum and ground to a very fine powder.
The only variation between RHC and regular Portland cement is the amount of limestone (tri-calcium silicate) used as a raw ingredient that provides the cement with its high early strength.
Mixing:
The aforementioned basic components are combined using the dry process to create RHC.
The materials are first crushed and reduced to tiny fragments.
They are then dried in drying kilns, usually with less than 1% water content.
In a ball mill the dried materials are ground into tiny particles.
Grinding and Burning:
The components are combined in the right amounts, and then the mixture is heated up and burned.
Here, the chemicals undergo a series of reactions to transform into the calcium silicates that make up cement clinker.
A tiny amount of gypsum is added while the pellets are processed in ball mills or tube mills after they have cooled.
Gypsum serves as a retarder in cement.
Composition of Rapid Hardening Cement:
When we look at the constituents of cement, we can see that it is made up of calcareous (calcite), siliceous (silicate), argillaceous (clay), and other substances.
In general, the following constituent proportions are included.
A cement’s total weight is composed of 60% tricalcium silicate (C3S), 15% dicalcium silicate (C2S), and 10% tricalcium aluminate (C3A), and 8% tetra calcium aluminoferrite.
C3S makes up 50% of the total weight of OPC, therefore it can be seen that the composition of Rapid Hardening Cement comprises a higher percentage of C3S than OPC.
Advantages of Rapid Hardening Cement:
- It is protected from sulphate assaults.
- When cement cures and hardens, shrinkage is reduced.
- Road pavements use this cement to enable early traffic opening and in colder regions, it is also employed in the production of precast concrete slabs, posts, and electric poles.
- As compared to cement, it achieves high strength quickly and the formwork can be removed earlier.
- It is an extremely durable cement that fits the quick speed of building and the tight budgets needed to complete projects.
Disadvantages of Rapid Hardening Cement:
- RHC shouldn’t be applied to water-retaining or submerged structures like dams and dikes.
- RHC is a hydraulic cement that produces a lot of heat during the hydration process.
- Shrinkage cracks can be produced when this quick hydration process comes into touch with a significant amount of water.
- Over time, this can lead to reinforcement rusting and shorten the lifespan of the concrete building.
- RHC should be avoided when mass-concreting massive concrete structures because it generates a lot of heat.
- As a result of the extreme heat difference between the structure’s internal and external portions, cracks are produced.
- The RHC is 10% more expensive than the OPC, hence it is costly.
Applications for Rapid Hardening Cement:
- It is utilized in situations where formwork needs to be removed as soon as feasible so that it can be reused.
- When high early strength is necessary.
- It is typically employed while building road pavements where it is crucial to swiftly open the road to traffic.
- Because moulds can be swiftly released, it is employed in companies that produce concrete goods like slabs, posts, electric poles, block fence, etc.
- Since of the quick generation of heat during hydration, which prevents the concrete from freezing, it is utilized for cold weather concreting.
Also read: Quick Setting Cement | Types of Cement | Hydrophobic Cement
Conclusion:
Within the first 24 hours, rapid hardening cement reaches a double strength of OPC cement.
Rapid-setting cement needs to be stored in a cool, dry environment.
Related Posts
Rock Quality Designation(RQD): Building Strong Foundations
Spread Footing
Masonry Cement
Plain Cement Concrete
Concrete Efflorescence
Concrete Pile
Stepped Footing
Fineness Modulus of Coarse Aggregates
Difference between Condo and Apartment