Agricultural waste materials such as rice husk ash (RHA) can be used in place of cement to produce concrete that is stronger, more workable, and less susceptible to corrosion of the steel reinforcement.
For a reasonable improvement of concrete, enhancing the use of cement raw materials must be maintained.
RHA is a highly responsive pozzolanic material that is used to replace regular Portland cement.
Utilizing RHA in concrete is a wise choice because it will improve the workability of the concrete.
In this article you’ll learn:
So, if you’re ready to go with rice husk ash in concrete, this article is for you.
Let’s dive right in.
What is Rice Husk Ash Concrete?
The burning of rice husk causes RHA.
The silicate deposits, which make up the majority of the evaporable components of rice husk are gradually lost during consumption.
The arrangement of the rice husks, the consumption temperature, and the consumption time all affect the characteristics of the debris.
For instance, a heater using 100 kg of husks will produce about 25 kg of RHA.
Properties of Rice Husk Ash Concrete:
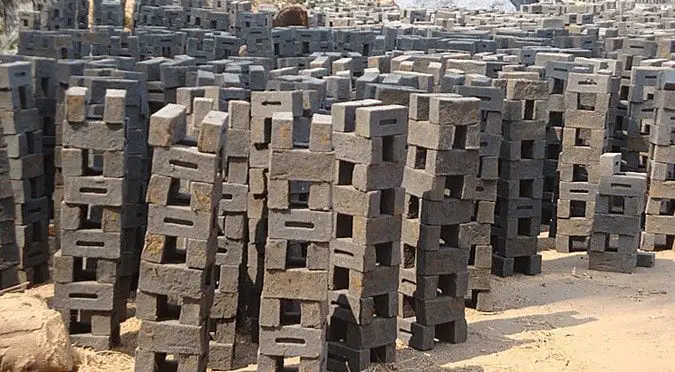
- The suitability of rice husk ash as a cementitious material was assessed using the physicochemical analysis of the constituents and the impact of RHA on concrete properties (fresh state and hardened state).
- The chemical analysis of RHA revealed that silica makes up almost 80% of its composition.
- To assess the properties of the fresh stage, workability measurements were taken for varying RHA percentages of concrete mix at a temperature of 320 C in terms of Slump (mm), Vee-Bee Degrees (sec.), and compaction factor. The results were analysed.
- The characteristics of hardened materials’ compressive strength, split tensile strength, and flexural strength was evaluated.
- A water absorption study was carried out to evaluate the sample’s effectiveness in terms of water absorption.
- The experimental investigation’s findings indicated that, in aspects of workability and strength, a replacement of close to 10% for rice husk ash in cement was ideal.
- The possibility of obtaining more carbon credits automatically rises when rice husk ash is used in place of cement in concrete to reduce greenhouse gas emissions to a greater extent.
Chemical Composition of Rice Husk Ash:
The chemical makeup of the rice husk ash is similar to that of many organic fibers are as follows:
- Lignin Cellulose (C5H10O5) (C7H10O3)
- Hemicellulose
- Holocellulose
- SiO2
The rice husk ash can vary from site to site and the processing method.
In order for the rice husk to have the right properties, it is treated by being burned.
Methods of Rice Husk Burning:
As was already mentioned, the kind of burning process used has a significant impact on the quality of rice husk.
Burning is done in a variety of ways, some of which are listed below:
1. Field Burning in the Open:
Poor quality rice husk ashes are produced by this method of open-burning rice husk ash.
These result in highly crystalline, less reactive form structures.
2. Burning in a Fluidized-Bed Furnace:
This is a controlled method of rice husk burning. Rice husk combustion produces heat that is converted into electricity.
The controlled operation is performed by keeping the time-temperature parameter constant range of 500 to 700 degrees Celsius.
This is done for a longer period of time to ensure that all of the carbon is removed.
In contrast, the temperature is increases from 700 to 800 degrees Celsius for a minute.
Rice husk ashes produced by the fluidized bed furnace method contain 80-95 percent silicon dioxide, 1-2 percent K2O, and 3-18 percent unburned carbon.
This approach is suggested for both financial and environmental reasons.
3. Industrial Furnace:
This method is proposed for both environmental and economic reasons.
The combustion efficiency would produce silica dioxide in the 90 – 95 percent range.
Utilizing amorphous silica and cellular building blocks in this process makes it simpler to produce rice husk ashes.
This method produces pozzolanic rice husk ash.
Advantages of Rice Husk Ash Concrete:
- Rice husk ash gives good compressive strength.
- It helps to lower pollution in the environment.
- It is a superior pozzolanic admixture or supplementary cementitious material due to its high silica content.
- This concrete has an impervious microstructure that offers better protection against sulphate attack, chloride ingress, carbonation, and other environmental factors.
- Concrete made from rice husk has better shrinkage characteristics and is more durable.
Disadvantages of Rice Husk Concrete:
- Concrete gradually becomes unworkable when rise husk ash is used.
- Due to the ease of placement and compaction, water-reducing admixtures must be used to produce workable concrete.
Uses of Rice Husk Ash Concrete:
- Rice husk ash improves the toughness of self-compacting high-performance concrete.
- The macro-mesoporous structure of rice husk ash makes it a suitable admixture for modifying viscosity.
- On self-compatibility and compressive strength, fly ash and rice husk ash work in concert.
- When released into the environment, rice husk ash (RHA), is produced that causes damage to the surrounding area and the land where it is dumped.
- The ignition cycle removes the natural products during the conversion of rice husk to ash, leaving behind silica-rich residues.
Also read: Sand Lime Bricks | Types of Bricks | Fly ash Bricks | Refractory Bricks | Clay Bricks
Conclusion:
The ideal percentage of RHA in concrete is 15% because it has a strength of less than 20 MPa.
The split tensile strength of conventional concrete was found to be 1.526 MPa, while the split tensile strength of concrete containing 15 % rice husk ash was found to be 1.697 MPa for 28 days.
It demonstrates a 24.41% improvement over traditional concrete.
Finally, we discovered through experimental analysis that it is beneficial to replace rice husk ash with cement in cement concrete to the extent of 15%.
Related Posts
Rock Quality Designation(RQD): Building Strong Foundations
Spread Footing
Masonry Cement
Plain Cement Concrete
Concrete Efflorescence
Concrete Pile
Stepped Footing
Fineness Modulus of Coarse Aggregates
Difference between Condo and Apartment