Special concrete is described as concrete that satisfies unique performance and uniformity standards.
The standards are not necessarily routinely achievable by utilizing the standard components and customary mixing, laying, and curing procedures.
In this article you’ll learn:
So, if you’re ready to go with it, this article is for you.
Let’s dive right in.
Introduction to Special Concrete:
The most important material in modern construction is concrete.
In addition to normal concretes, several types of concretes are also used including coloured, self-compacting, lightweight, high density, fibre reinforced, and polymer concrete.
Its production involves both art and science, it is made using unconventional methods with exceptional qualities referred to as special concretes.
It can come in a variety of shapes by definition a composite material made up primarily of a binding agent and an aggregate particle.
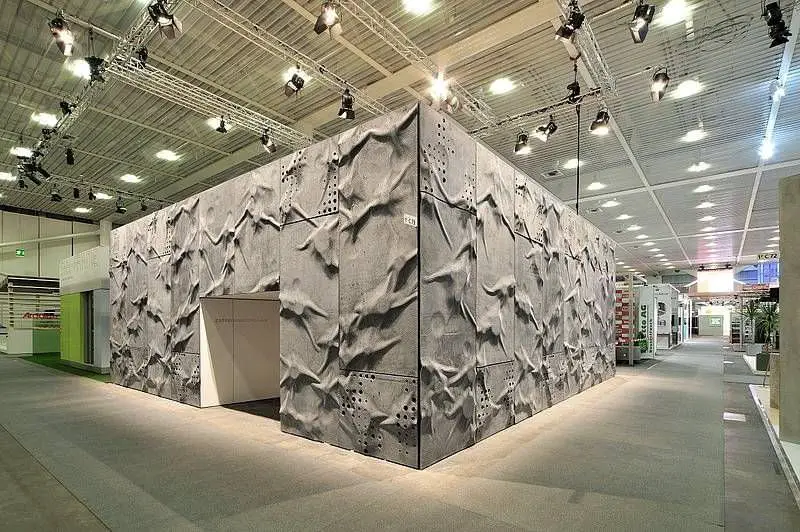
Types of Special Concrete:
1. High Volume Fly Ash Concrete:
It is utilized to partially substitute Portland cement for the mixture.
According to IS: 456 – 2000, fly ash may replace OPC as a binding material up to 35% of the time.
Over 35% of fly-ash is utilized as a substitute in HVFAC because of a variety of circumstances, including:
- 110 million tonnes of fly ash are produced in India each year, which is a lot.
- Fly ashes from large TPP are of extremely high grade or fly ash quality.
- Within 200 kilometres of a TPP, the cost of fly ash is just 10 to 20% of the price of cement.
- Environmental aspects, such as a decrease in CO2 emissions.
2. Silica fume concrete:
It is generated as a by-product in electric arc furnaces is extremely fine nanocrystalline silica.
Pozzolan is very reactive used to make mortar and concretes better.
Silica fume has two different effects:
- The physical impact.
- The chemical impact.
There is a thin layer known as the transition zone that sits between the big, moist cement paste and the aggregate particles.
The most porous section is also the weakest part of the material.
Through its physical and chemical actions, silica fume has a big impact on the transition zone.
3. Ternary blend concrete:
Three separate cementitious ingredients such as blends of Portland cement, slag cement, and a third cementitious substance are used to make ternary concrete.
Fly ash is frequently the third component, but silica fume is also typical.
Currently, Portland and slag cement are not usually utilized in conjunction with other ingredients such as rice husk ash.
In ternary combinations, slag cement has been utilized for many years.
Ternary mixtures can be applied to practical application as follows:
- Concretes with high performance.
- Cast-ahead concretes.
- Units are made of masonry and brickwork.
- Shotcrete.
4. Self-Compacting Concrete:
Self-Compacting Concrete is a special kind of concrete that flows under its own weight and fills formwork voids without the need for mechanical vibration.
It is utilized in situations when mechanical vibration devices have difficulty compacting concretes.
5. Lightweight concrete:
Lightweight concrete is a type of concrete that is less packed and heavier than other types of concrete.
The difference between structural lightweight and regular weight concretes is its decreased density.
It is built with thin aggregates.
The density between 1350 and 1850 kg/m3.
After 28 days, compressive strength of greater than 17 MPa.
The main purpose is to lessen the dead-load weight of the members like floors in tall buildings.
6. Fibre Reinforced Concrete:
Fibre Reinforced Concrete unique type of concrete is made by combining concrete with extra fibers.
It is made with materials including steel, glass, nylon, polypropylene, and vegetable fibers.
By wrapping themselves around the aggregate, additional fibers make it harder to work.
The mixtures become more cohesive and less prone to segregation.
It has a variety of fibers such as charcoal, jute, asbestos, glass, polypropylene, nylon, steel, and other materials.
It has rounded or flattened filaments.
For fibers, the aspect ratio ranges from 30 to 150, or the length of fibre/diameter is crucial.
7. Polymer concrete:
A polymer concrete uses polymers as a binder in addition to or instead of cement.
Some of the variants include polymer-impregnated concretes, polymer concretes, and polymer-Portland cement concretes.
Due to their great thermal stability and chemical resistance, thermosetting resins are employed as the main polymer component.
Aggregates made of silica, quartz, granite, limestone, and other premium materials are also included.
Since typical concretes is porous, it has poor strength.
Ordinary concrete’s porosity is decreased and its strength is increased by adding a polymer or monomer.
It has different varieties:
- Concretes infused with polymers (PIC)
- Concretes made of Polymer Cement (PCC)
Polymer Concretes (PC) has been surface-coated and partially impregnated.
8. Colored concrete:
Concrete can be colored by employing colored aggregates, adding color pigments (ASTM C 979), or a combination of both.
After casting, there must be a wait of around two weeks if surfaces are to be acid washed.
Natural rocks like quartz, marble, granite and ceramic materials can be used as colored aggregates.
In general, synthetic pigments produce more consistent effects.
When added to mixture, color pigments shouldn’t make up more than 10% of the cement mass.
For instance, a pigment dose equal to 1.5% of the mass of cement may provide a nice pastel color, but it may take up to 7% to create a deep color.
9. Temperature Controlled Concrete:
Controlled concrete is prepared with strong quality control while also considering the design strength, workability, and durability into account.
In the first laboratory, various combinations are created and tested using the recommended design approach.
The ratio of cement to fine aggregate, grading, water content, workability, and capacity requirements are all set of mix.
10. GGBS, Slag-based concrete:
GGBS (Ground Granulated Blast-furnace Slag) is a cementitious substance that is a by-product of the blast furnaces used to make iron.
About 1,500 °C is the operating temperature of blast furnaces, which are supplied with a precisely regulated mixture of limestone, coke, and iron ore.
The ultimate strength with GGBS cement is higher than that of Portland cement.
As compared to Portland cement, it contains more calcium silicate hydrates (CSH), which increase strength, and less free lime.
11. Mass concrete:
A significant amount of cast-in-place concretes with dimensions necessitates taking precautions to deal with heat generation and the resulting volume change to reduce cracking.
In addition to low-cement concrete used in dams and other large projects, mass concrete also contains concrete with moderate to high cement concentration utilized in bridge and building structural components.
As the internal concretes warms and expands, it’s possible that the external concretes is cooling and contracting.
The temperature difference, the physical characteristics, and the reinforcing steel affect the wide and deep fissures.
12. Pervious concrete:
The ingredients of pervious (porous or no-fines) concretes are a narrowly graded coarse aggregate, little or no fine aggregate, and insufficient cement paste to fill coarse aggregate voids.
It has a low water-to-cement ratio and low slump is kept together by cement paste.
They are produced with a high percentage of voids (20–35%) and a high permeability that makes it simple for water to pass through.
Pervious concrete is used in parking lots, pavements, airport local groundwater supplies, and hydraulic projects as a drainage medium because it allows water to permeate the concrete to the ground beneath.
Tennis courts and greenhouses have both utilized previous concretes.
Diverse blends can have compressive strengths ranging from 3.5 to 27.5 Mpa.
Advantages of Special Concrete:
- Since particular conditions are maintained throughout the preparation, it makes the construction more durable than standard concretes.
- Extreme weather and tough environmental conditions are suited for special concretes.
- Special concretes exhibit low thermal properties.
- In these concretes, the components can be changed to change the setting time which is not feasible because each has a specific set time depending on the mix design.
- Special concretes can prevent corrosion of the reinforcements.
- Some speciality concretes are ideal for cold climates because of their outstanding thermal qualities.
Disadvantages of Special Concrete:
- It has a low tensile strength when compared to other binding substances.
- They are less ductile.
- When compared to its strength, the weight of the comparison is heavy.
- Soluble salts may be present, but the salts in the solution lead to efflorescence.
Applications of Special Concrete:
- It is used in radioactive locations because it may absorb radiation, it serves as a shield to stop the radiation from seeping outside and endangering people’s lives.
- Shotcrete has several uses on curved surfaces where conventional technologies make it challenging to lay concretes like vertical surfaces, tunnel lining, reservoirs, swimming pools, etc.
- It can be utilized in chimneys, furnaces, refractories, and other high-temperature applications.
- The finishing of floors and the dismantling of wall systems both employ vacuum concrete.
- It is utilized by manufacturers that create precast plain and reinforced units.
- Bridge abutments, retaining walls, maritime buildings, canal locks, dams, and other structures require mass concretes.
Conclusion:
Special concrete are rapidly growing in favor of the building sector due to their unique properties.
The mechanism is expensive, so further study is needed before it can be applied more broadly.
Special concretes are frequently utilized in affluent nations because the cost is not a significant consideration, however, it plays a significant role for developing and poor nations.
Related Posts
Rock Quality Designation(RQD): Building Strong Foundations
Spread Footing
Masonry Cement
Plain Cement Concrete
Concrete Efflorescence
Concrete Pile
Stepped Footing
Fineness Modulus of Coarse Aggregates
Difference between Condo and Apartment