Vacuum concrete is a mixture of concrete in which extra water is drawn out to increase concrete strength.
A fluid mix with a water-cement ratio of 0.50 to 0.65 is required to facilitate the placement and compacting of thin sections of concrete, such as slabs and walls.
Such a mixture will produce materials with poor abrasion resistance and relatively low strength.
In such a situation, the vacuum treatment of concrete, which entails sucking extra water and air out of the concrete, can be helpful.
When a vacuum treatment system for concrete draws air through a surface attached to a vacuum pump.
In this article you’ll learn:
So, if you’re ready to go with vacuum concrete, this article is for you.
Let’s dive right in.
Introduction to Vacuum Concrete:
Trimix AB developed vacuum concrete, it was later granted an American patent and gained popularity across all of Europe.
This method is currently used in almost half of the concrete construction projects in Sweden.
In 1987, Aquarius Technologies became the first company to use this method in India.
In order to strengthen the material, vacuum concrete has extra water removed from it. Vacuum materials attached to a vacuum pump are used to remove the water.
Technique and Types of Equipment for Vacuum Concrete:
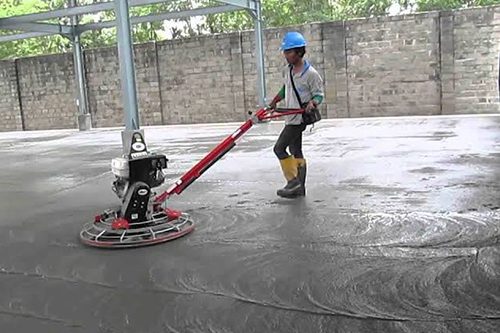
The technique’s primary goal is to use vacuum dewatering to remove extra water from concrete surfaces.
Dewatering significantly lowers the effective water-cement ratio, which significantly enhances concrete performance.
On the surface, there has been more improvement where it is most required.
Vacuum dewatering of concrete primarily requires the following four elements as listed below:
- Vacuum Pump.
- Separator Of Water.
- Filtration Pad.
- Board Vibrator for Screed.
- Pump For Vacuuming Forms with A Hose.
- Vacuum Mat.
- Energy Float.
A vacuum pump is a small, but powerful 5–10 HP pump, while vacuum extraction and storage of the water in the water separator.
The mats are positioned on top of tiny filter pads, which stop water from washing cement away.
The contraction in the total volume of concrete is properly controlled by the magnitude of the water removed.
The concrete layer’s thickness is decreased by almost 3%.
A rigid backing sheet, expanded metal, wire gauze, or muslin cloth sheet make up a filtering pad.
Additionally, a rubber seal is attached to the filtering pad.
Working Process of Vacuum Concrete:
The ratio of water to cement and the standard of the water to be removed determine how long the treatment will take.
In general, slabs with thicknesses varying from 25 mm to 125 mm take 1 to 15 minutes.
When a treatment’s effects start off stronger than they eventually become and fade away quickly, therefore it serves no purpose to extend the length of the treatment beyond these figures.
The vacuum treatment is not very effective for a water-cement ratio of less than 0.4, when the pressure in the atmosphere is approximately one-third that on the concrete.
Concrete can be helped by vibration before vacuum treatment.
After initial vibration, it is very effective to apply vibration while also treating with a vacuum and concrete structure may be harmed if vibration persists after 90%.
Therefore, after this time the vibrations should stop, and for the remainder of the treatment, only a vacuum to be used.
The time required for the final finishing of the floor and the removal of all forms has been found to be significantly reduced by the vacuum treatment.
When the overall shrinkage of concrete is reduced, its strength and resistance to wear and abrasion increase.
A strong band between the top layer of concrete and vacuum-treated concrete is created.
Precast reinforced and plain concrete units have been manufactured in large quantities using processed concrete.
Other significant horizontal and sloping concrete slab constructions include floor slabs, pavements for roads and airports, thin load-bearing walls, and partitions.
It can also be used to replace, resurface, and repair road pavement.
How to Lay Vacuum Concrete in Steps:
The formwork is filled with a sufficiently workable concrete mixture.
A needle vibrator compacts the concrete’s surface after it has been laid.
A double beam screed vibrator is used to perform further compaction.
In this case, a smooth surface is created.
Following compaction, vacuum dewatering is initiated using vacuum equipment:
- Vacuum mat.
- Pad filters.
- Vase pump.
The 4″ (inch) filter cover is left exposed on all sides as the filter pads are positioned on the recently laid concrete.
The exposed concrete surface left by the filter pads is covered by the top cover, which is put on top of the filter pads.
The suction hose from this top cover connects to a vacuum pump.
The vacuum pump is then turned on for 15 to 25 minutes depending on thickness of the concrete floors.
Within the perimeter of the mat and top cover, a vacuum is immediately produced as the pump runs.
From an economic perspective, the time required for pumping is typically 15 to 25 minutes.
Pumping for longer than 30 minutes results in a negligible decrease in water content and it should be avoided.
The concrete is compressed by atmospheric pressure, and excess water is drawn from it by suction through a fine wire gauge/muslin cloth.
The results are as follows:
- 15 to 25% less water than before was present in the mixture.
- 3% less concrete layer depth.
- For every cm of floor thickness, dewatering takes 1.5–2 minutes.
This dewatered concrete is compacted and dried until it cannot be walked on without leaving a trace.
This dried concrete suggests that the concrete has been adequately dried.
After being skim-floated, the concrete surface is hardened and smoothed with the aid of a power trowel and power floater.
This re-vibrate helps to clear the capillaries or channels created by the suction of the water.
The dewatered surface offers ideal conditions for receiving powdered hardeners increasing the concrete’s resistance to abrasion.
Advantages of Vacuum Concrete:
- Vacuum dewatering allows for the simultaneous achievement of high strength and workability of concrete.
- A reduced water-cement ratio may result in a 10 to 50% increase in compressive strength and a reduction in permeability.
- It increases the concrete surface’s abrasion resistance.
- The surface created by vacuum dewatering is plain and smooth because there is less shrinkage.
- The surface can be used sooner after the formwork has been removed.
Disadvantages of Vacuum concrete:
- They require particular tools.
- This requires skilled labour.
- They require energy to use.
- They cost a lot upfront.
- Concrete’s porosity makes it possible for water, oil, and grease to seep through, which weakens the material.
Application of Vacuum Concreting:
- In the manufacturing company for precast PCC and RCC units.
- Sloping and horizontal concrete slabs.
- Building workshops and warehouses.
- Canals.
- Railings for trains.
- Airport sidewalks and docks.
- walls with a low load capacity.
- Parking lots and cellars.
- Road pavement repairs and resurfacing.
- Hydropower facilities.
Also read: Reactive Powder Concrete | Lime Concrete | Bendable Concrete | Plum Concrete
Conclusion:
Vacuum concreting is a method for removing extra water to increase strength while increasing workability.
Compacting of concrete with a water-cement ratio greater than 0.4 is also possible.
It has many uses in slabs where increased workability is crucial.
Related Posts
Rock Quality Designation(RQD): Building Strong Foundations
Spread Footing
Masonry Cement
Plain Cement Concrete
Concrete Efflorescence
Concrete Pile
Stepped Footing
Fineness Modulus of Coarse Aggregates
Difference between Condo and Apartment