A concrete plant also known as a batch plant or batching plant or a concrete batching plant, is equipment that combines various ingredients to form concrete include water, air, admixtures, sand, aggregate (rocks, gravel, etc.), fly ash, silica fume, slag, and cement.
Batching of concrete could be achieved by either weight batching or volume batching.
Here we will learn about batching plant, types of batching plants & much more.
Introduction to batching plant:
A batching plant is a machine for the manufacture of concrete from its ingredients such as cement, crushed stone, sand, water, and admixture chemical.
Sometimes ingredients such as GGBS, fly ash or micro-silica are added to modify the characteristics of the final product.
The term batching plant comes from “batch” which means concrete is manufactured in measured bathes inside a concrete batching plant.
Objective of batching plant:
- Better quality concrete is produced.
- Elimination of storage space for basic materials on site.
- Ending the procurement/recruitment of plant and machinery.
- Wastage of basic materials is avoided.
Types of Concrete Batching Plant:
1.Transit Mix Plant / Dry Concrete Batching Plant:
The transit mix plant makes use of manual or digital scales to aggregate and weight the cement.
Water can also be weighed or measured separately, after weighing the fabric is poured into a transit mixer, which is transported to the location.
All materials are blended during transportation to the construction site.
Water is added either to the location or throughout transportation, relying on the situation of the plant or site.
2.Central Mix Plant / Wet Concrete Batching Plant:
Central mix requires all the ingredients together with water, the materials are mixed in a mixer situated at a central location within the plant.
After the mixing process, the concrete is poured into the shifting truck which delivers to the location.
The truck should transfer quickly so that the concrete does not freeze.
3.Stationary Concrete Batching Plant:
Stable concrete batching plants are steady and situated in a long way from the construction site.
Concrete is transported to the construction site using a truck; steady concrete batching plants are simple to set up, they are bigger in dimension than cellular concrete batching plants.
They are excessive effective and produce high-quality concrete & care must be taken that the truck reaches the location on the desired time.
Otherwise, the concrete will start to freeze, due to this fact the inferior concrete can be distributed.
Stationary concrete batching plants are generally used for industrial projects with large span and enormous demand for concrete.
4.Mobile Concrete Batching Plant:
Sometimes the stationary concrete batching plant is situated at distance that the price of transporting the concrete will increase, therefore becomes more economical.
In such circumstances, mobile concrete batching plants are extra popular with physical storage, weighing, mixing and discharging models.
After setting up the plant, the contractor can modify concrete manufacturing according to the job requirement.
After the construction is over, this plant is moved to a different site..
By using mobile concrete within the stationary plants, delay in transport of vans could be avoided, however, this batching plant has low effectiveness and capability.
If the material is not weighed correctly, the concrete won’t obtain the specified strength and the durability of the structure decreases.
For small scale projects, manual batching could be achieved.
Advantages of batching plants:
- A centralized concrete batching plant can serve a large space.
- The plants are situated in areas for industrial use and supply trucks can serve residential districts or inside cities.
- Better quality concrete is produced.
- Elimination of storage space for basic materials on site.
- Elimination of hiring of plant and machinery.
- The wastage of basic materials is avoided.
- Workers associated with the production of concrete are eliminated.
- The time required is greatly reduced.
- Noise and dust pollution on the site is reduced.
Disadvantages of batching plants:
- Materials from central plant and mixing begins at that plant, so the travel time is crucial over long distances.
- The access road and site access must be not able to carry a greater load of ready-mix trucks.
- It has limited-time between mixing and curing of the concrete is 210 minutes of batching.
Batching Plant Process Flow Chart:
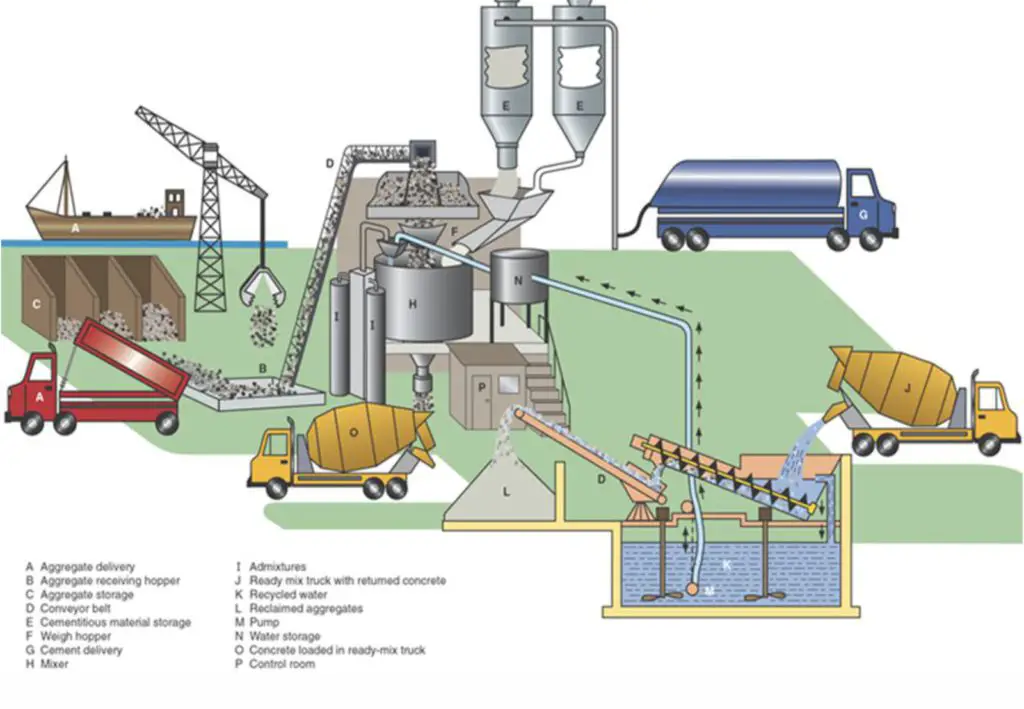
Application of Batching Plants:
In Ready Mix:
A concrete plant also known as ready mix concrete plant is usually located inside the city and concrete is transported to the site by a concrete truck mixer.
Ready-mixed concrete plants are required for the durability, reliability, safety and environmental protection of concrete plant systems.
In Precast Applications:
Precast concrete is a concrete product that is processed in a homogeneous process in the manufacturing unit.
With cast-in-place concrete, precast concrete can be produced in batches and cured.
Precast concrete batching plants have a safe construction environment, low prices, and high-quality materials.
It is also used in transportation, construction, water conservation and various fields.
Also read: Cooling Tower & Surge Tank
Conclusion:
The batching plant will produce a very limited amount of waste and materials.
A concrete recycling machine will be installed on-site to recycle concrete waste to reduce material consumption and waste generation.
well done, thanks