Ready mixed concrete is an ideal concrete that is manufactured in a factory or in a batching plant based on standard required specifications; Ready-mixed concrete is a mixture of Portland or other cement, water, and aggregates: sand, gravel, or crushed stone.
The finished concrete mixture is then transported to the worksheet within the transit mixer above the truck.
Here we will learn about ready mixed concrete, types of ready mix concrete & much more.
Introduction to ready mix concrete:
Ready mixed concrete (RMC) is a ready to use materials with a prearranged combination of cement, sand, aggregates and water.
The idea of Ready Mix Concrete (RMC) was first introduced by the architect Jurgen Heinrich Magens.
In 1907, he found that the time available for transport could be increased not only by cooling fresh concrete, but also by vibrating throughout transport.
Objective of ready mixed concrete:
- Higher quality concrete is produced.
- Elimination of space for storing for primary materials on site.
- Dissipation of primary materials is prevented.
Types of Ready Mixed Concrete:
1.Transit Composite Concrete:
Transit composite concrete is also called dry-batch concrete because all the essential components are immediately charged in the truck mixer.
The mixer drum is quickly rotated at the charging speed during the loading and after it is rotated at conventional mixing speed.
In such ready-mix concrete, three types of adjustments are also possible.
2.Shrink Mixed Concrete:
In shrink-mixed concrete, the concrete is partially mixed in the plant mixer and partially mixed in a truck-mounted drum mixer during transit time.
The amount of mixture within the transit mixer depends on the amount of mixture carried out at the central mixing plant.
Tests need to be performed to establish the need for mixing of drum mixers.
3. Central Mixed Concrete:
Central mixed concrete is also known as a central batching plant, where the concrete is added accurately before loading into a truck mixer, they are also called wet-batch or pre-mixed plants.
Sometimes, non-agitating units or dump trucks will also be used, when reasonableness is required or leads are low.
material used in Ready Mixed Concrete:
Aggregates:
They are important materials in concrete, they occupy 70–80% of the volume of concrete, the aggregates are divided into two categories by consideration of size:
Aggregates bigger than 4.75 mm are considered as coarse aggregate, with a dimension of 4.75 mm or less is considered a fine aggregate.
Cement:
Cement is composed of four main compounds: Dicalcium Silicate (2Ca0 Si.), Tricalcium silicate (3Ca0 Si02), Tricalcium aluminate (3Ca0 Al203), Tetra-Calcium aluminoferrite (4Ca0 Al203 Fe203).
These compounds are designated as C2S, C3S, C3A, and C4AF, where C stands for calcium oxide (lime), S for silica and A for alumina and iron oxide.
Small quantities of alcohol and magnesia are additionally present, as well as minor quantities of alkalis and other elements.
Fly ash:
The coal used in plants is mainly composed of combustible elements such as carbon, hydrogen and oxygen and non-combustible impurities (from 10 to 40%) commonly present as clay, shale, quartz, feldspar and limestone.
The size of fly ash ranges from 1.0 to 100 microns and the average size is about 20 microns.
Water:
The pH value of water should be between 6.0 and 8.0 according to IS 456-2000.
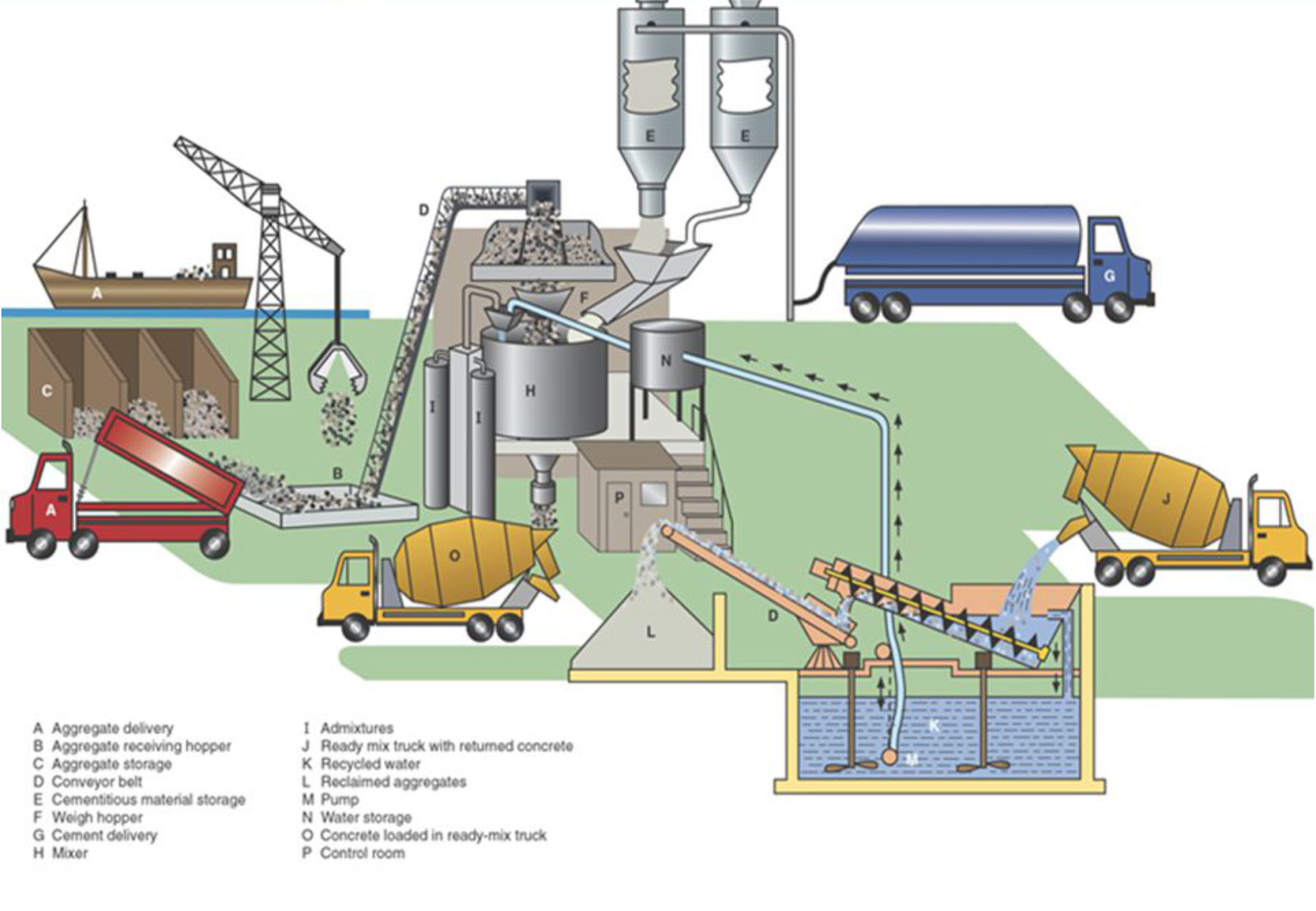
Advantages of ready mixed concrete:
- Quality concrete is obtained from a ready-mixed concrete mix plant that uses advanced equipment and stationary methods.
- There is strict control over material testing process constraints and continuous monitoring are the key practices throughout the construction.
- In the case of site mix concrete, poor management over the enter materials, batching, and mixing methods are resolved within the ready mix concrete methodology.
- In the construction works to be adopted within the ready mix concrete plant, the speed after the mechanical operation is fixed.
- The output from the site combines the concrete plant using an 8/12 mixer which is 30–60 metric cubes per hour to 4-5 metric cubes per hour within the ready mix concrete plant.
- Better handling and proper mixing will help in reducing cement consumption by 10 – 12%.
- Also, the use of admixture and various materials will help to reduce the amount of cement.
- Concrete mixes are used with high versatility, these are the best concrete methods.
- Cement is shielded and dust is minimized because the finished concrete uses a bulk mixture of concrete instead of a bag of cement.
- Conservation of cement will conserve energy and resources: due to low consumption, cement production is low hence environmental pollution is low.
- Thus an extra durable structure is obtained, which will increase service life and saves costs.
- In the manufacture of ready-mix concrete, there may be much less dependence on human laborers, so the probabilities of human errors are lowered, dependence on intensive laborers also decreases.
- Small or massive quantities of concrete are delivered on time as per specification.
- There has been no delay due to site-based batching plant erection or dismantling; no equipment rental; no depreciation of value.
- Consumption of petrol and diesel is low, hence noise and air pollution are reduced.
Disadvantages of Ready Mixed Concrete:
- Transit time might from the time of preparation of concrete on the distribution site, might affect the performance.
- There is a need to add extra water or penetration to maintain functionality according to the specification.
- On-site, quality assurance (QA) / quality control (QC) has to test functionality through fatigue testing before being used for manufacture.
- Traffic during the transit of concrete might result in the setting of concrete so the addition of entrances is required to delay the setting period.
- Formwork and placing arrangements should be prepared in a big area in advance as concrete might be bought in large portions.
Difference between Ready Mix Concrete & Site Mix Concrete:
Ready Mix Concrete | Site Mix Concrete |
The standard is fixed quality of concrete made in high-tech batching plants in computerized environments. | The standard is inconsistent as a result of the concrete is combined by hand. |
Construction in double-quick time. | Manual mixing is time-consuming, so tasks take longer time to finish. |
Raw materials are selected after strict high-quality checks. | The quality of raw materials is manually checked or not checked. |
Large quantities of concrete may be ordered, this lets you upgrade yourself and deal with various tasks. | Repeated mixing must be finished in large quantities because the mixer can be too small to deal with the requirement. |
There is no such thing as wastage of raw materials on your site, everything is pre-mixed in our plants, relying on your needs. | Excessive wastage of raw supplies due to manual mixing. |
Safe work practice, no disruption to your schedule. | Extremely unsafe, unskilled, and untrained labourers may work negligently leading to harmful working circumstances. |
You don’t have to stock the materials and watch them, there is no worry about the pilgrimage. | The danger of pilgrimage to raw materials is excessive. |
Also read: Difference between concrete and cement
Application of Ready Mixed Concrete:
- Foundation.
- Building.
- Highway.
- Bridge.
- Walkway.
- Retaining wall.
- Airport.
- Tunnels.
- Canals.
- Pile Foundation.
- Water tank.
- Shear wall.
- Kerb.
- Dams.
- Power Plant.
Also read: Hardened concrete, Fresh concrete & Self Healing Concrete
Conclusion:
The concrete quality produced by the Ready Mixed Concrete plant offers a higher strength when hardened and the efficiency of the construction.
RMC operation is extremely mechanized and managed entirely via electronic control which reduces the possibility of errors in various tasks.
It’s interesting that you mention that ready mix concrete can be used to build a retaining wall. I want to have a retaining wall added to my property this summer, so I’m considering buying some ready mix concrete for it. I’m going to look for a good business in my area that sells ready mix concrete.
Thanks for pointing out that since ready mixed concrete uses stationary methods and advanced equipment, quality concrete is obtained. My plan is to have a new driveway installed next weekend. Since I want the installation to be done efficiently and using quality materials, I will consider ordering ready mix concrete.
Nice! This is really going to help out the people do the right thing about concretes and avoid the mistakes.
What you said about the benefit of using ready-mixed concrete, that the constructor could control it in the material testing process to monitor the construction, is true. The mixing method can reduce spill to 10 percent is a considerable saving of money, especially if you are on a budget. My friend is planning to construct a new house here in Lee’s Summit, MO, next month, and what I learned about ready mix concrete will help my friend choose the suitable material where she can save money.
It’s very helpful to know that ready-mix concrete is used due to its high versatility. Not long ago, one of my friends told me he’d like to renovate his house’s backyard and build a patio with a fire pit, so he’s interested in finding the right material for the project, and I believe he’d be interested in reading your information. Thanks for the insight on ready-mix concrete and how it reduces the amount of cement used.
Thank you for explaining some of the benefits and advantages of ready mixed concrete. I’ve been wondering what kind of concrete we should use for our project. I’ll be sure to keep this in mind so we can make a good decision about what to use.