Blended cement is a homogeneous blend of normal Portland cement (OPC) with additives including silica fumes, fly ash, limestone, and slag to enhance the quality of the cement for diverse purposes.
Concrete’s workability, strength, durability, and chemical resistance may be increased by using blended cement.
In this article you’ll learn:
So, if you’re ready to go with it, this article is for you.
Let’s dive right in.
What is Blended Cement?
Blended cement is created by combining Portland cement with supplemental cementitious materials (SCMs) at temperatures between 1400 and 1500 °C, such as fly ash from the burning of coal in power plants or blast furnace slag from iron-making sites.
One or more additives are mixed together during the manufacturing process.
Purpose of Blended Cement:
- Improved workability and pumpability are two of the qualities acquired by combining cement with different components.
- It decreases the water demand.
- Also improves the bleed control.
- It reduces drying shrinkage and creep.
- Sulphate resistance and chloride penetration have been enhanced.
- Decreased Alkali Aggregate reaction potential.
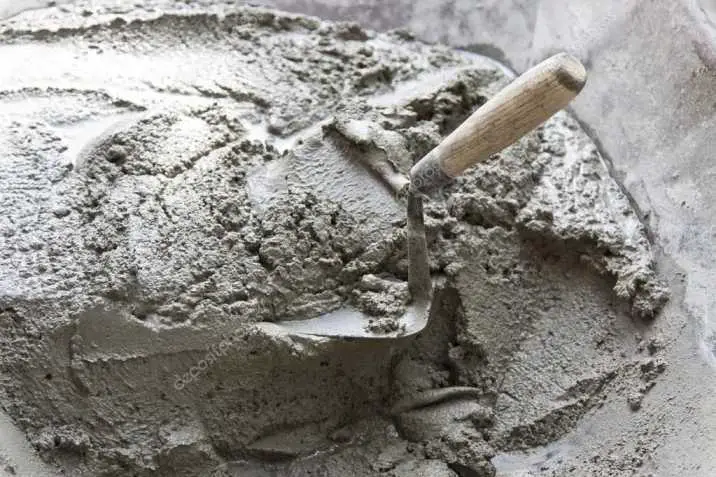
Types of Blended Cement Concrete:
The type of blending ingredient used in the cement impacts the classification.
Thus, according to American Society for Testing and Materials (ASTM) criteria, this cement is classified into four types:
1. Type IS (X), Portland-Slag Cement:
Portland Slag Cement or PSC is blends with up to 70% slag cement are used for typical constructions.
Slag is a non-metallic material that contains silicates, alumina-silicates of lime, and more than 90% glass.
It has these characteristics:
- Concrete has greater compressive strengths than OPC.
- Since of its higher flexural strength, concrete has a more rigid structure and experiences fewer load deflections.
- As of its poor permeability, it reduces the infiltration of hazardous compounds such as chlorides and sulphates.
- Environmentally favourable owing to lower GHG emissions.
2. Type IP (X), Portland-Pozzolan Cement:
Portland Pozzolana Cement is created by either grinding OPC clinker, gypsum, and pozzolanic components separately.
Then, it is thoroughly blending them in predetermined proportions, or by grinding OPC clinker, gypsum, and pozzolanic ingredients simultaneously.
This blend is used for ordinary construction that include up to 50% pozzolana.
The most frequent pozzolan used in mixed cement is fly ash.
It has these characteristics:
- High compressive strength is present.
- It protects concrete from the alkali-aggregate reaction.
- Increases the concrete’s permeability and density.
3. Type IL (X), Portland-Limestone Cement:
Portland-limestone cement (PLC) is a blended cement with a higher proportion of limestone.
It operates, measures, and functions just like regular cement, but has an estimated carbon footprint that is 10% lower.
It is utilized in mixed designs in the same way that standard Portland cement that may be produced at any Portland cement plant.
Ordinary Portland cement (OPC) can have up to 5% limestone, whereas PLC has between 5% and 15% limestone.
It has the following characteristics:
- Improves durability.
- Excellent placement and finishing abilities.
- Shrinkage and hydration heat were improved.
- Improved strength and setting performance.
4. Type IT (X), Ternary Blended Cement:
Blended Ternary Cement (IT): Fly ash, slag cement, or silica fume are two complementary additional ingredients that are combined to form ternary cement.
It should be noted that the kind of blend is determined by the largest amount of material in the mix.
For example, if fly ash was the most abundant component, it would be classified as Type IP.
The letter “(X)” in the designation denotes the proportion of the constituent in the blended cement.
Type IL (10, Portland-limestone cement, for example, includes 10 percent limestone and 90 percent Portland cement).
Ternary is made up of three distinct cementitious elements.
It has these characteristics:
- Extreme Resilience.
- A Lack of Corrosion.
- Resistance to ASR.
- Thermal cracking is eliminated.
- Permeability is low.
- Resistance to sulphates.
Advantages of Blended Concrete:
- It creates a finer texture when mixed and applied than OPC, therefore finishing and elevation projects can use it.
- Water consumption is low, making it simple to work with shape.
- In both compressive and flexural stress, the strength obtained after 28 days is much more than OPC.
- When compared to regular cement, blended concrete has a low permeability that extends the life of the concrete by minimizing the penetration of hostile water run-off components such as sulphates and chlorides.
- It reduces cracks caused by thermal stress caused by temperature variations.
- By using this cement mix of silica fume and fly ash or slag, Alkali-Silica Reaction problems were lessened.
Applications of Blended Cement:
- Domestic building and major engineering projects.
- In exceptional durability and an off-form finish are required.
- Road construction requires stabilization, which includes pavement recycling.
- Mining.
Also read: Soil Cement | Hydraulic Cement | Quick Setting Cement | White Portland Cement
Conclusion:
Blended cement is environmentally friendly and performs well.
The use of supplementary cementitious material blended with Portland cement is due to various performance measures such as low permeability, resistance to chlorides and sulphates, improved workability, etc.
Related Posts
Rock Quality Designation(RQD): Building Strong Foundations
Spread Footing
Masonry Cement
Plain Cement Concrete
Concrete Efflorescence
Concrete Pile
Stepped Footing
Fineness Modulus of Coarse Aggregates
Difference between Condo and Apartment