Pipe joints in the water supply are vital components of a plumbing system that connect multiple pipes.
There are many different types of pipe joints, but the choice of one depends on factors like pipe size, material, flow pressure, and others.
Each pipe’s pressure should be able to withstand the pipe joint.
In this article you’ll learn:
So, if you’re ready to go with a pipe joint, this article is for you.
Let’s dive right in.
What are Pipe Joints in Plumbing?
Pipe joints are used to connect pipes in any piping system because a pipe network cannot have a constant length of pipe.
Due to the technology used to create the joint, these joints have the potential to make or break a pipeline system in terms of durability.
The pipeline industry uses a variety of pipe materials depending on the need and type of products that will be transferred through the pipes.
Purpose of pipe joints:
- Pipe joints are the interconnection at the ends of pipes that enable the connection of pipes of various lengths.
- Joints give the pipeline strength because longer pipeline sections have a tendency to bend.
- Pipe joints are required in any piping system because a pipe network cannot have a consistent length of pipe.
- These joints have the power to make or break a pipeline system depending on the durable jointing technique.
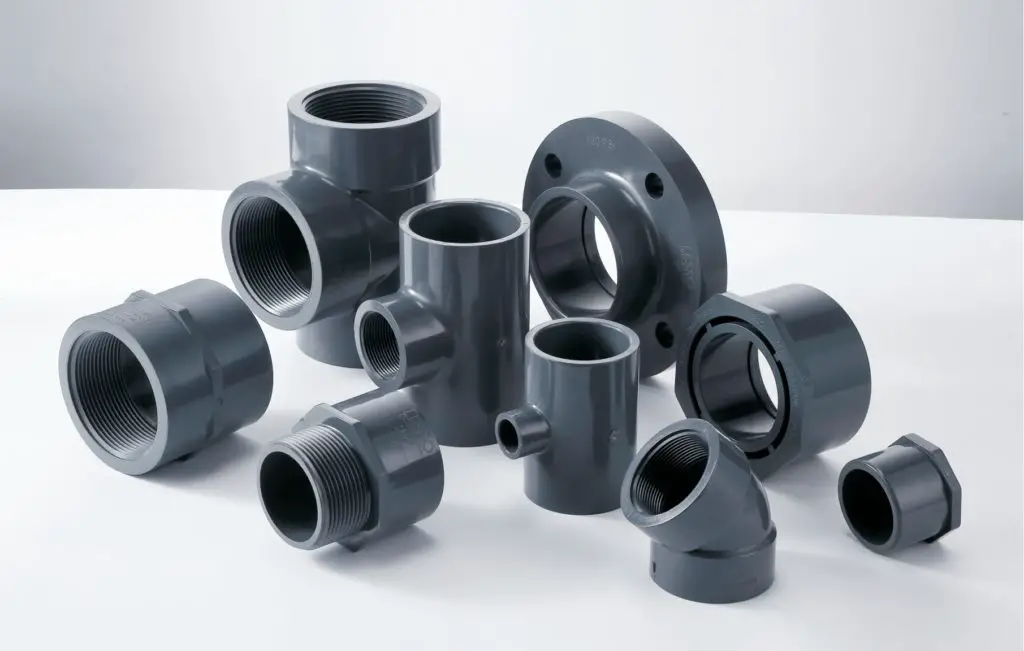
Types of Pipe Joints in Plumbing:
1. Pipe Threaded Joint:
A threaded joint are screwed together using threads that are built into each pipe.
Threads run along the inside of one pipe while running along the outside of the other.
There are threaded cast iron, copper, PVC, and G.I. pipes available.
There are threaded joints for pipes with a diameter of 6 mm to 300 mm.
For low temperature and low-pressure flows, they are preferred.
The joints may expand and leak in hotter areas as a result of thermal expansion.
Threaded joints are simple to install, but they need to be well-maintained.
2. Brazed Joint in Pipe:
Brazing is a method of joining pipes that uses molten filler material at temperatures higher than 840oC.
Typically, copper or copper alloy pipes are joined using brazing.
Tin has a strong affinity for copper, makes up the majority of the filler. However, due to its flaws, tin is often combined with other substances like nickel, bismuth, silver, and copper.
Parent metal should have a higher melting point than filler metal.
Brazed joints have lower mechanical strength than other joints.
In regions with a moderate range of temperatures, this type of pipe joints is appropriate.
3. Pipe Soldered Joint:
The only difference between soldering and brazing is that the filler metal melts at lower temperatures in the case of soldering.
Soldering is also used to connect pipes made of copper and copper alloy.
Pipes and fittings are coated with paste flux before soldering to protect them from oxidation caused by flame.
For installation, we also need skilled laborers.
Low-temperature areas can use soldered joints.
As brazed joints, these have low mechanical strength.
4. Pipe Butt Welded Joint:
It is necessary to weld the pipes together when their diameters are the same.
This is most popular kind of welding and installing the joint requires skilled personnel.
Typically, large commercial and industrial piping systems use these joints.
Since of the smooth, continuous surface inside the joint, a butt weld gives the joint good strength that can withstand high pressure.
Internal weld backing rings can be used to join the pipe more cost-effectively than butt weld joints by using less filler material.
But under extreme pressure, these rings might crack and break.
The joints cannot be opened for maintenance because they are fixed.
The external smoothing of the welded portion will improve the piping system’s appearance.
5. Pipe Socket Welded Joint:
Socket welded joints are used when there is a high likelihood of joint leakage.
Pipes are joined by inserting one into another and the joint is then welded.
Pipes with various diameters work well in this kind of joint.
When pipes are the same diameter, the necessary fittings are used.
In general, welding is less expensive than butt welding.
When compared to butt welded joints, socket welded joints have lower fatigue resistance.
However, when compared to other mechanical joints, socket welded joints produce good results.
6. Pipe Flanged Joint:
High pressure flows and large diameter pipes both use flanged joints.
In general, they are utilized with threaded or plain end pipes to stop leaks, two flange parts are fastened together by bolts at the pipe joint.
Typically, cast iron, steel is used to make these joint, they are strong and durable under high pressure.
The fixing of bolts should be done properly while installing as high temperatures that can cause them to fail under creep and lose their grip.
They are also helpful for maintenance and pipe joints repairs.
7. Pipe Compression Joint:
Compression joints are used to join pipes that have plain ends when fittings are installed at the ends of the pipes.
Threaded couplings or fittings will be used to join the ends of the pipes; therefore, pipes of various materials and sizes can be connected.
However, the joints must be properly sized to withstand flow pressure; otherwise, they could breakdown and leak.
Compression fittings come in a variety of materials, and the choice of fittings may depend on our needs.
8. Pipe Grooved Joint:
In a grooved joint, the pipe ends have grooved edges that are connected by an elastomer wrap, and the elastomer seal is then locked in place by grooved couplings made of ductile iron.
Bolts are used to connect these grooved couplings.
These joints are inexpensive and simple to install.
Due to thermal expansion, grooved joints allow for some axial movement while providing good pressure resistance.
However, elastomer seals may lose their strength and experience torsional failure in high-temperature areas, therefore designated as areas with moderate temperatures.
For pipe maintenance, grooved joints are preferred because they are simple to remove.
9. Piping Expansion Joint:
These highly engineered mechanical devices also referred to as Expansion Bellows, contain one or more metal/rubber bellows
Expansion joints are used to soak up dimensional changes brought on by a pipeline, duct, or vessel’s thermal expansion or contraction while maintaining system pressure.
The flexible part of the expansion joint known as a bellows expands or contracts to make room for thermal movement.
Expansion joints are successfully used in refineries, chemical and petrochemical plants, cryogenic plants, nuclear power plants, automobiles, aerospace, and heating and cooling systems.
10. Exhaust Flexible Joint:
Flex joints and exhaust bellows are made specifically for the engine exhaust market.
We will not be able to take any long drives and would have to walk every day to work.
The flex joint is situated between the telescopic joint and the bottom of the diverter to guards your engine from malfunctioning as you accelerate down the road.
Advantages of Pipe Joints:
- The risk of leakage is significantly reduced when pipe fittings are used in place of threaded fittings.
- For weld preparation, a pipe does not need to be bevelled.
- The pipe bore cannot be entered by the weld metal.
- Since there are no strict fit-up requirements and no need for specialized machining for butt weld end preparation, construction prices are reduced than to butt-welded joints.
Disadvantages of Plumping Joints:
- For UHP pressure applications in the food industry, socket weld pipe fittings are unacceptable because they do not allow for full penetration, leave overlaps and have difficult-to-clean crevices that effectively create leaks.
- For socket weld pipe fittings, there needs to be an expansion gap of 1/16 inch (1.6 mm) between the pipe and socket shoulder.
- Systems that are socket welded have internal crevices and an expansion gap encourages corrosion and limits their suitability for corrosive or radioactive applications.
- Problems with operation or maintenance may result from solid build-up at the joints.
Also read: Types of Pipes | Plumbing Trap | Types of Valves
Conclusion:
Pipe joints are essential component of any piping or plumbing system.
Depending on the nature, a piping assembly employs a variety of joints or joining techniques.
In most cases, the pipe joints can withstand the piping pressure.
When choosing a pipe joint, a number of things need to be taken into account including material price, cost of installation labour, required level of leakage integrity, requirements for routine maintenance, and specific specifications for performance.
Related Posts
Rock Quality Designation(RQD): Building Strong Foundations
Spread Footing
Masonry Cement
Plain Cement Concrete
Concrete Efflorescence
Concrete Pile
Stepped Footing
Fineness Modulus of Coarse Aggregates
Difference between Condo and Apartment