Operators of compaction rollers involved in road construction are often faced with danger as they deal with surfaces that are sloped. Any operator would attest to the fact that each degree of a slope is felt significantly by them.
The safety of crewmembers involved in road construction is paramount, and manufacturers are taking the results of a recent OSHA investigation into account. Certain safety features could save lives during rollover incidents.
Each time operators contend with sloped road shoulders or ditches, they increase the risk of a rollover.
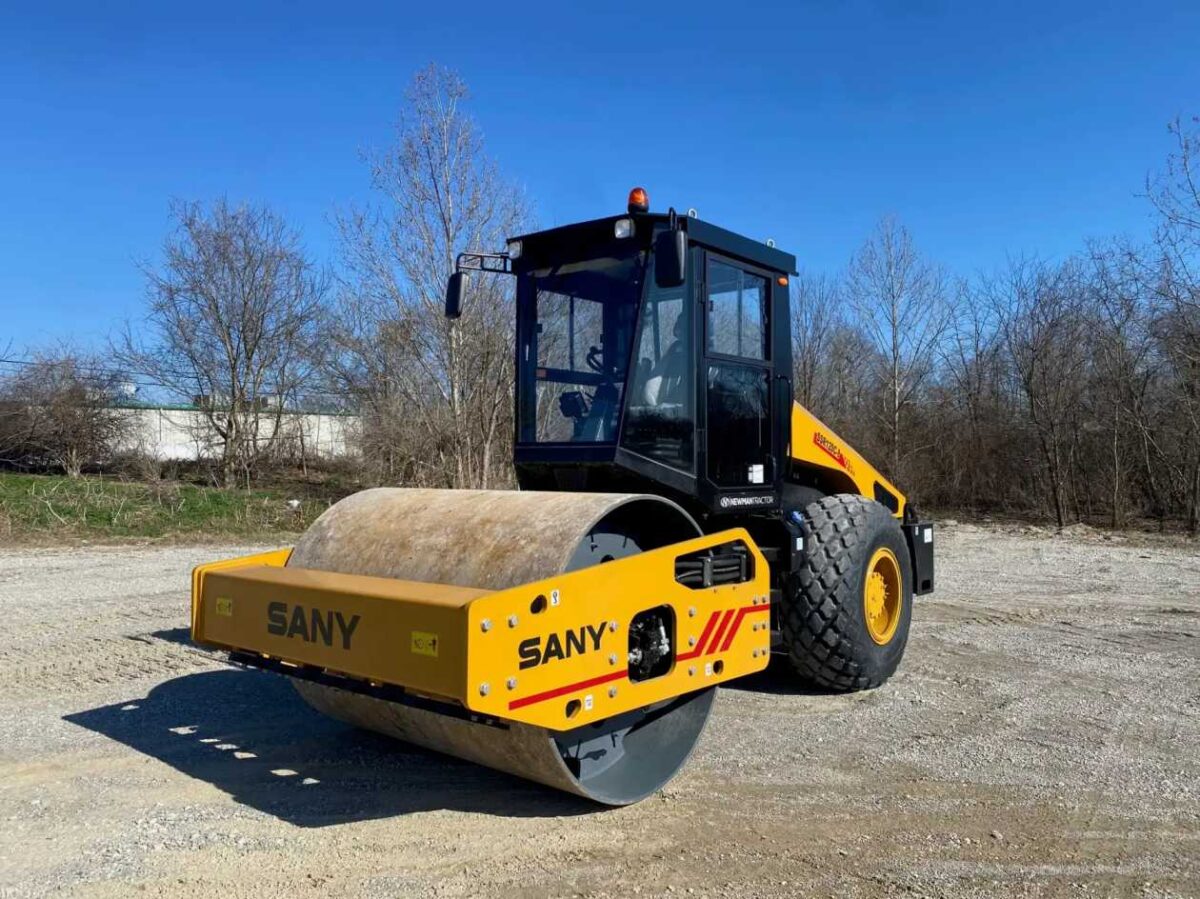
Recent research or rather investigations by OSHA according to Anthony Davis, the managing editor of ‘Highways Today’ have revealed that safety elements have shown the ability of safety features such as ROPS (Rollover Protective Structures), seatbelts, and basic PPE (Personal Protective Equipment) which include hard hats and safety boots can save lives in the event of a compaction rollers accident, however, these safety features do nothing much in terms of preventing an accident.
This revelation has triggered a renewed interest in the design and development of compaction rollers that move away from the current flawed platform associated with high risk, high maintenance, and lower utility levels towards leasing roller compactor rental machinery that is safer and carries lower maintenance costs.
In essence, according to the article by Highway Today, manufacturers have taken the primary obstacles that are associated with conventional compaction rollers and redesigned them from scratch.
The renewed interest in the design of roller compactors is focused more than anything else followed by lower ownership costs and easier maintenance.
According to the publication, the primary issue associated with the lack of safety of these machines was the use of the compaction drums for not just motion and compaction, but also as the element of stability for these machines.
The safety issue that arises from this configuration is easily resolved by relocating the drum to offset arms and apart from this with the attachment, these machines can also be connected to other tools that allow operators to perform other tasks whilst enhancing the stability of the machine directly attributed to the offset arm.
In essence, with the new configuration operators are able to maintain the machine on flat ground while the extended arm extends towards sloped areas which reduces the chances of rollover incidents as relocating the drum to offset arms improves safety drastically and enhances the utility level of the machine significantly.
By separating the compaction rollers and rendering it as a separate system, the drum is no longer an on-board component which means maintenance requirements are reduced drastically.
The extended arm features a universal mounting mechanism (hydraulic connections) that allows operators to set and disconnect hydraulic tools to the host machine easily and quickly.
Also read: Sheepsfoot Rollers
Hydraulic compaction rollers attachments basically have no components to maintain other than clearing debris and greasing there are no other maintenance requirements such as oil changes, transmission fluid changes, or mechanical parts to replace due to wear and tear.
Related Posts
Rock Quality Designation(RQD): Building Strong Foundations
Spread Footing
Masonry Cement
Plain Cement Concrete
Concrete Efflorescence
Concrete Pile
Stepped Footing
Fineness Modulus of Coarse Aggregates
Difference between Condo and Apartment