A Slump test is a laboratory or site test that is used to measure the consistency of concrete; a slump test shows signs of uniformity of concrete in different batches, the shape of the concrete slumps shows the information of the workability and quality of the concrete.
The slump test is a way to measure the workability of concrete.
It is defined as the difference between the height of the concrete before removing the slump cone (mold) and the height of the concrete after removing of slump cone as measured during the concrete slump test.
Slumps have various applications as it can imply something about the nature of the concrete while it is still fresh.
Long ago, a 3–4-inch slump was considered ideal for workability because it was less challenging to work and much more slump meant too much water.
But within the last 40–50 years, admixtures (additives to the concrete) have been developed that will allow massive slumps without loss of cohesion or segregation.
Slump Test Procedure:
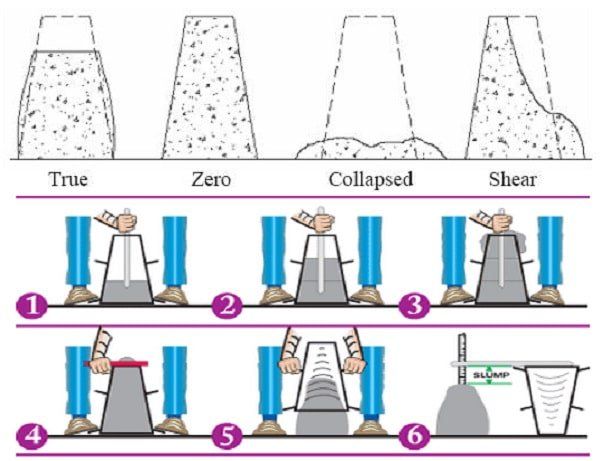
Slump Test is the most common to test the consistency or workability of concrete.
The “slump cone” is a sheet metal “frustrated” cone, 300 mm tall, bottom diameter is 200 mm, and the top diameter is 100 mm, it is placed on a stable surface, usually made of steel.
The cone is fitted with small steel tabs at the bottom; the operator stands on those tabs to hold the cone firmly on the surface.
Concrete is placed into the cone with the 3 layers, each being compacted in turn with 25 “rods” of a 16 mm diameter, a bullet ended rod.
After compaction is done, the concrete is struck off at the top and excess cement is wiped away from the outside of the cone, especially lying on the surface.
In slump test, operator firmly holds the cone down manually, carefully steps away from the cone & then carefully lifts the cone and places it inverted adjacent to the concrete.
The tamping rod is placed on the top of the slump cone, so that it runs across above the mound of concrete.
A steel ruler is used to measure down from the underside of the rod to the average height of the top of the concrete, value is recorded as the “slump.”
Values can range from 0 to 250 mm is seen very rarely i.e. in the case for concrete with superplasticizer or self-compacting concrete, or concrete with 7 mm maximum particle size.
Slump Test Values:
- Very low workability: slump value 0-25mm or 0-1 inch.
- Low workability: slump value 25-50mm or 1-2 inches.
- Medium workability: slump value 50-100mm or 2-4 inch.
- High workability: slump value 100-175mm or 4-7 inches.
Also read: CBR test, RQD, COD & BOD
Conclusion:
The slump test is a way to measure the workability of concrete.
A small slump means the concrete is stiff; a massive slump implies the concrete will flow easily.
The slump test is performed by packing a metal cone with the concrete according to a specified procedure, then lifting the metal cone off the pavement and measuring the fall of the top of the concrete.
Related Posts
Rock Quality Designation(RQD): Building Strong Foundations
Spread Footing
Masonry Cement
Plain Cement Concrete
Concrete Efflorescence
Concrete Pile
Stepped Footing
Fineness Modulus of Coarse Aggregates
Difference between Condo and Apartment