A centrifugal pump is a mechanical device designed to move fluid by means of the transfer of rotational energy from one or more driven rotors called impellers. The fluid enters the fast-moving impeller along its axis and is ejected by the impeller force through the impeller tips along its circumference.
This moves the water radially outward at high velocity, causes the water to rise to higher levels.
Here we will learn about centrifugal pump, types of centrifugal pump & working of centrifugal pumps.
Centrifugal Pump Working Principle:
It works on the principle of forced vortex flow when a certain mass of the fluid is increased by the external torque in the pressure head.
The conversion of energy is based on two main parts of the pump: a) the impeller b) the casing.
The impeller converts the conductive energy into kinetic energy and the casing converts kinetic energy into pressure energy.
Types of Centrifugal Pump:
Classification of centrifugal pump based on the range of the working head as follows:
1.Low Head Pump (up to 15 m head):
Typically, these pumps do not have guide vanes.
2.Medium Head Pump (15 m to 40 m head):
They are usually provided with the guide vanes.
3.High Head Pump (> 40 m head):
These are multistage pumps as an impeller pump cannot create pressure more than 40 head.
Classification od centrifugal pump based on the size of the casing used as follows:
4.Volute Pump or Constant Velocity Pump:
A pump with a volute or collection of water passing through the impeller of the slowly rising area from the cutwater on the distribution pipe.
The cross-section is designed to give a constant velocity in a spiral-shaped curly it is also called constant velocity solute.
The energy loss is greatly reduced if employed compared to a circular casing.
This increases the efficiency of the pump slightly.
5.Vortex or Variable Velocity:
The volute pump has a relatively larger diameter than the pump to provide an annular space between the impeller and the solute passage.
In this annular space called the vortex chamber, there is a free vortex in which the velocity of flow of liquid falls from the impeller outlet to the inlet of the solute passage.
Radial pressure increases from the centre to the outside, due to the decrease in velocity.
Volute pumps and vortex volute pumps are single-phase pumps with horizontal shafts.
6.Diffuser Casing:
In this casing, the guide vanes are held at the outlet of the impeller.
Guide vanes are designed to offer a regularly increased path for the flow of liquid.
The kinetic energy of the liquid of the impeller is converted into strain energy throughout flow within the guide vanes.
Classification of centrifugal pump based on the multiple impulses that use pumps per shaft as follows:
7.Single-stage Pump:
It has an impeller suitable for heads up to 40 meters.
8.Multistage Pump:
These pumps use two or more number of impulses in series.
In these pumps, the discharge of a pump from the casing enters the eye of the impeller of the next pump in series.
The total head developed by the multistage pump is equal to the algebraic sum of the head developed by each pump.
Classification of centrifugal pump based on the disposition of the shaft:
9.Horizontal Pump:
In this types of pumps, the impeller shaft is used horizontally.
10.Vertical pump:
In this pump, the impeller shaft is used vertically.
Classification of centrifugal pump based on the number of stages:
11.Single-phase:
In single-phase pumps, only one impeller is used on the shaft.
12.Multi-stage:
In multi-stage pumps, more than one impeller is used on the same shaft and enclosed in a single casing.
Classification of centrifugal pump based on types of impeller:
13.Closed Impeller:
If the vanes of the impeller are covered with plates on both sides, it’s known as a closed impeller.
It is the product of cast iron, stainless steel, and cast steel.
14.Open impeller:
If the impeller vane is without a cover plate, it is known as an open impeller.
These are usually the product of solid steel.
15.Semi-open impeller:
If the impeller’s vanes are covered with a plate on one side, it’s known as a semi-open impeller.
It has a smaller number of vans, however, its height is increased than that of a closed impeller.
Classification of centrifugal pump based on the number of impeller penetration:
16.Single suction pump:
The liquid only enters the impeller through the suction pipe.
17.Double suction pump:
The liquid enters both sides of the impeller.
Working of Centrifugal Pump:
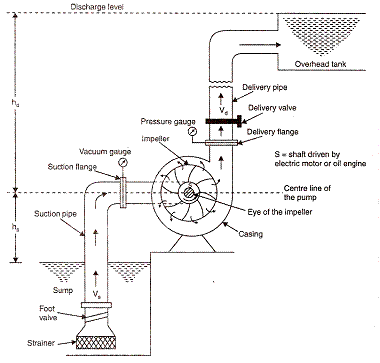
The steps involved in operating a centrifugal pump are as follows:
- The delivery valve of the pump is closed.
- The priming of the pump is done. (priming includes filling the fluid in the suction pipe up to the level of the delivery valve so that the no air pockets persist in the arrangement)
- The pump shaft and impeller are now rotated with the help of the external motor or any other mover, the rotation produces the forced vortex, and vacuum on the impeller eye causes the liquid to rise from the sump into a suction pipe.
- The speed of the impeller must be sufficient to produce the centrifugal head.
- Now the delivery valve is opened then the liquid is lifted and discharged through the delivery pipe due to high pressure.
- Before stopping the pump, it is essential to close the delivery pipe otherwise there may be a backflow of liquid from the high head reservoir.
Advantages of Centrifugal Pump:
- Centrifugal pumps are small in size, space-saving & fewer capital costs.
- They are easy for maintenance.
- Also, deal with large volume.
- It is able to work with medium to low heat.
- It is used for low viscosity fluids.
- Also, have a high power to weight ratio.
- They have safe air intake.
- It has maximum pressure during start-up and shutdown.
Disadvantages of Centrifugal Pump:
- These pumps produce cavitation.
- They undergo corrosion.
- It cannot able to work at high speed.
Applications of Centrifugal Pump:
They are used for supplying water, boosting pressure, pumping water for domestic requirements, assisting fire protection systems, hot water circulation, sewage drainage and regulating boiler water are the most common applications.
Some of the major sectors that make use of these pumps are described below:
Water desalination plants:
In 2025, UN estimates that 14% of the global population will be suffering from water scarcity.
As such water desalination plants are vital, they involve separating various minerals and dissolved salts from unusable water.
Also potable pumping water can be transferred to areas that need it most.
Mining industry:
Mining pumps are involved in the processing of minerals.
They help separate valuable minerals from bitumen, gangue and process minerals.
During the mining process, the centrifugal pump are used to transport the solid containing fluids and slurries.
Petrochemical plants:
This industry relies heavily on centrifugal pumps.
The robustness of centrifugal pumps is important for the value of petrochemical components produced.
Through well designed centrifugal pumps the production of rubbers, plastics and dyes are done.
All these industry operations are heavily dependent on centrifugal pumps.
Also read: Concrete Pump, Reciprocating Pump & Submersible Pump
Conclusion:
The centrifugal pump is usually used for a commercial purpose because they transport of liquids with relatively high speed.
These pumps has an easy shape so it’s ultimately cost-efficient.
Related Posts
Rock Quality Designation(RQD): Building Strong Foundations
Spread Footing
Masonry Cement
Plain Cement Concrete
Concrete Efflorescence
Concrete Pile
Stepped Footing
Fineness Modulus of Coarse Aggregates
Difference between Condo and Apartment